Zero Emissions Doesn’t Mean Zero Opportunities
The fate of the internal combustion engine is sealed. While it has played a key role in the technological progress of the 20th Century, it is time to move onto greener modes of transport. Road transportation is responsible for an estimated 12%-15% of global greenhouse gas emissions.
Vehicles powered by electricity are here to stay, and whatever powertrain dominates and how quickly they replace their fossil-fuel ancestors is cause for speculation. But it’s happening, and it’s happening fast.
Despite the pandemic, demand for EVs has grown rapidly in Europe and China. In the United Kingdom, Europe’s third-largest car market, registrations of all vehicles slowed to a trickle in April 2020, falling to 4,321 from 254,684 in March. Since then, sales have recovered, and the market share of alternative fuel vehicles (including battery EVs and hybrids) has steadily increased, too. EVs now outsell diesels.

Elsewhere in Europe, 71% of new vehicle registrations in Norway in 2021 were electrified vehicles.

In China, the world’s largest car market, overall vehicle sales for 2020 fell by 2% while EV registrations increased to 1.3 million from 1.2 million in 2019, then more than doubled in 2021. Analysts attributed the growth to a combination of extended incentives and people’s anxiety over using mass transit during the pandemic.
Global sales of passenger EVs reached 3.2 million units by the end of 2020, an increase of 41% over the previous year. By the end of 2021 they had passed 6 million. Bloomberg NEF projects EV sales will exceed 10.5 million by the end of 2022.

The promotion of zero-emissions transport continues the world over through incentives and tax breaks. It is cheaper to lease a new Tesla than an equivalent-sized used BMW in California.
This all adds up to a stark reminder for producers of passenger car motor oil that demand for factory fill lubricants is slowing and service fill will succumb as well.
Legislative Push
The auto industry was sent reeling in July 2021 when lawmakers of the European Union, the world’s largest trading block, unveiled its aim to become the first climate-neutral continent by 2050. This plan includes reducing net greenhouse gas emissions by at least 55% by 2030, in line with the United Nations 17 Sustainable Development Goals.
One way this can be achieved is to ban sales of ICE cars, something the European Car Manufacturers’ Association said was “not rational” in a press statement in July 2021.
At the same time, United States President Joe Biden’s administration signaled that the U.S. is ready to play ball on reducing emissions, too, when he called a zero-emission transport summit at the White House in August 2021 with the country’s legacy carmakers.
Detroit was quick to throw its weight behind the president’s goal of increasing the share of BEVs and plug-in hybrids in total car sales. Ford, GM and Stellantis (formerly Fiat Chrysler and PSA Group) released a joint statement on their goal of achieving a 50% share of EVs by 2030. BMW, Ford, Honda, Volkswagen and Volvo released a statement of support of their own, as did the United Autoworkers Union.
Many carmakers have over the past year finally committed to phasing out ICEs entirely. GM set things in motion with its announcement in January—albeit for passenger cars only—to give up gasoline in favor of BEVs by 2035.
Other manufacturers have yet to lay out specific time frames, but it is becoming increasingly clear that carmakers’ ICE vehicles will only have a tiny share in new car sales by the end of this decade, especially in Europe. Even legendary German sports car company Porsche has laid out plans to that end.
Bloomberg notes that while policy is important, demand is being driven harder by organic consumer demand.
EV Fluid Requirements
As with all machines, EVs need lubricants to reduce friction, corrosion and wear. But there are further challenges to formulators of e-fluids. They include the presence of high-voltage currents, electric motors that experience rotational speeds between 20,000 and 30,000 revolutions per minute, higher and more localized heat loads in batteries and gear reducers, and the ability to share fluids between parts of the vehicle, which all increase complexity.
EV lubrication can be grouped into three main applications: fluids for cooling batteries and electric motors; greases for e-motor bearings, wheel bearings and constant velocity joints; and transmission lubricants for reduction gears, differentials and direct lubrication of e-motor windings.
|
This means fluids must be able to tolerate high heat and have excellent heat transfer ability, corrosion resistance, dielectric strength and material compatibility with copper and insulation.
EV lubrication can be grouped into three main applications: fluids for cooling batteries and electric motors; greases for e-motor bearings, wheel bearings and constant velocity joints; and transmission lubricants for reduction gears, differentials and direct lubrication of e-motor windings. Many of the lube companies currently developing fluids optimized for EVs offer fluids in these three areas.
Battery Development
Many of the world’s biggest battery cell companies are announcing capacity expansions. CATL of China will add 92.5 gigawatt hours to an existing 65.45 GWh. South Korea’s LG Energy Solutions is set to triple current capacity of 155 GWh by 2025. Compatriots SK ON’s new plant in the United States will beef up annual capacity of 40 GWh to 220 GWh this year.
Current capacity and planned expansion add up to a thirst for thermal management fluids, as well as for such essential metals as lithium, cobalt and nickel.
Panasonic is working on an innovative and potentially game-changing cell that Tesla intends to use going forward. The cells claim an extra 16% range for the Model Y, built in Germany.

Elsewhere, Toyota, BMW, Ford, GM and Nio are all searching for a viable solid state battery—the industry’s holy grail. Compared with conventional lithium-ion batteries, solid-state batteries do not use a flammable liquid electrolyte and are considered safer. They also pack greater energy density without the extra weight, which in turn provides additional range.
The switch from lithium-ion batteries to solid state could have a significant effect on demand for not only thermal management fluids but also to a lesser extent for lubricants for extraction machinery in cobalt, nickel and lithium mines.
Thermal Management
A typical BEV thermal management system uses a water-glycol fluid pumped around the battery module in metal pipes, much like an ICE’s oil-based cooling system. This method is well-established and reliable, but it has certain limitations. They include a lack of heat-transfer efficiency, longer charging times and the need for anti-corrosion additives in the liquid.

Batteries can also be cooled by a non-conductive fluid in direct contact with the cells known as a dielectric. This method has a number of benefits, including up to four times faster heat transfer, which decreases charging times—Castrol claims by as much as 41% for its product. The method also offers reduced peak battery temperatures and lower risk of thermal runaway, as has been observed in indirect cooling systems. Some disadvantages of dielectric fluids are cost, vehicle safety in case of impact, and compatibility with battery components.
Dielectric fluids can be formulated from a range of base stocks, including mineral oils, silicones, esters, polyalphaolefins and even purified ion-free water.
Greases
EV greases are a second avenue for lubricant makers and additive companies hunting for opportunities in this emerging market. E-motors use rolling element bearings, so developing greases for BEVs could become a key area of interest.
The two main applications for greases in a BEV in terms of technical challenges are the wheel bearings and electric motors. Battery packs in current BEV designs put axles under higher loads. This means higher concentrations of non-conventional extreme pressure and anti-wear additives may be necessary. These higher loads mean higher bearing temperatures, which in turn may lead to more antioxidants in the grease.
The grease in a rolling element bearing must stay in contact with components without leaking due to gravity, centrifugal force or pressure. They must also retain their properties in this high temperature, high shear environment when revolutions per minute can reach their maximum.
Transmission Fluids
The third main lubricant application is in reducer gears. E-motors spin faster than is needed at the wheel, and reducer gears step down rotational velocities ranging between 20,000 and 30,000 rpm to around 1,200 rpm. This generates heat, which must be dissipated.
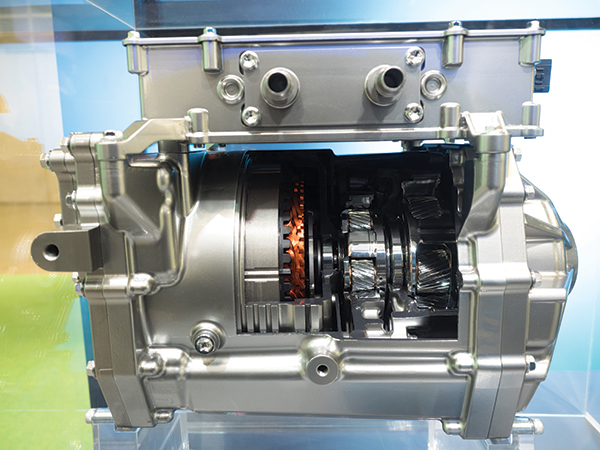
Opportunities
Each carmaker has a unique e-motor design, battery system and component materials. Additives required for BEV fluids have to be tailored to the specific physical challenges of electric drivetrains: high heat, high pressure and high rotation speeds.
The outlook for carmakers in 2022 is very rosy. China will account for around 50% of global EV sales, with the European Union taking 30%, and the U.S. and the rest of the world accounting for 20%. The market for electric buses and commercial vehicles is also rocketing, with sales of zero-emissions delivery vans and trucks growing by 75%, Bloomberg predicts.

Even though BEVs do not need liters of engine oil like an ICE, there still may be opportunities for lube blenders adjusting to the future of zero-emissions transport. As the tide is turning against hydrocarbons extraction—something that the world’s largest oil and gas companies are well aware of—lubricants of all kinds are less likely to be formulated with virgin mineral oil.
Instead, the market share of silicone, PAG, PAO, bio-based or rerefined mineral base stocks could grow, especially in the face of growing interest in creating a circular carbon economy.
This leaves lube makers hunting for market share in places where EV penetration is slower, such as Latin America and Africa, or focusing on other applications such as heavy-duty engine oil.
In this Spotlight, BASF and Lanxess share how they are contributing to an all-electric future.

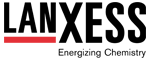
Materials for the Next Generation of Vehicles
Fueled by consumer demand, environmental pressures and stricter regulations, e-mobility is becoming increasingly important for a greener, more sustainable future. Automakers have to navigate the many complexities of battery electric vehicles (BEV), such as the need to reduce weight, optimize efficiency, improve driving range and cut charging times. LANXESS, with its expertise and a dedicated team of specialists, is ready to play its part.
BEVs are reliant on lithium-ion batteries that come in a range of different shapes, sizes and combinations. LANXESS produces numerous chemicals and materials that are used in the manufacture of battery cells. The specialty chemicals group is one of Europe’s leading producers of hydrofluoric acid and phosphorus chemicals—both key raw materials for the production of the high-purity conductive salt lithium hexafluorophosphate (LiPF6). LANXESS is also one of the world’s leading manufacturers of synthetic iron oxides, which serve as precursors to the low cost and sustainable cathode material lithium iron phosphate (LFP). LANXESS is also working on the environmentally friendly extraction of battery-grade lithium from brine and has signed a cooperation agreement with Guangzhou Tinci Materials Technology Co. for the production of electrolyte formulations in Leverkusen, Germany.
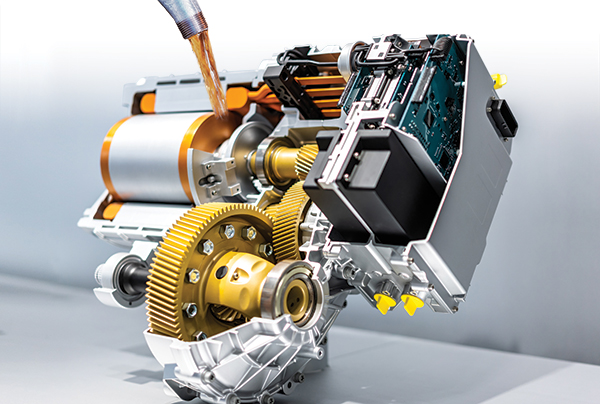
For applications beyond the battery cell itself, LANXESS offers high-performance plastics, e.g. for battery housings, HV connectors, overmolded busbars and applications in the charging infrastructure. The product range also includes flame retardants that are used in plastics and for non-flammable electrolytes to provide additional safety.
Furthermore, a shift in both buying habits and performance requirements in the automotive sector is steering specialty chemical companies, such as LANXESS, toward the development of innovative lubricants and thermal fluids for use in BEVs. Inevitably, these next generation vehicles bring their own challenges and will need optimized driveline and battery coolant fluids.
“Consumers are demanding BEVs that can be driven farther between charges and recharged quickly,” says Travis Benanti, technical manager and head of LAB process development at LANXESS. “OEMs are responding by using more Li-ion cells and higher voltages and currents to allow faster recharging. These trends mean increases in the rate of heat generated while fast-charging Li-ion batteries. Current methods of cooling Li-ion batteries may not be sufficient in future BEV configurations where charging may only take 20-30 minutes.”
Advanced Cooling
Current Li-ion battery technologies are large, heavy and expensive. They also are extremely sensitive to heat, which can negatively affect their performance.
Batteries are subject to temperature increases during charging and use. These effects are compounded by the tight packing of cells and their placement in an enclosure. To ensure reliability and longevity, Li-ion batteries should ideally remain at about 15-35°C (60-95°F) and not exceed 60°C. They can suffer irreversible damage at 90°C, leading to safety concerns.
Most BEVs currently use water-glycol mixtures that pass through a system of pipes and heat exchangers to cool the batteries (indirect cooling). However, direct immersion cooling (DIC)—using a non-conductive fluid in direct contact with the battery cells—is widely seen as a more effective solution moving forward. DIC allows for higher cooling capacity, which leads to more uniform battery temperatures and enables faster charging times.
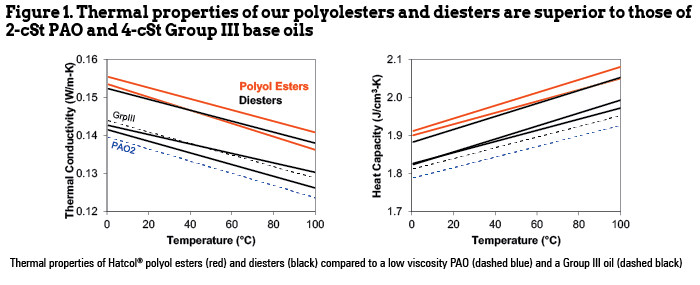
The success of DIC technology largely depends on the quality of the thermal fluid, and there are clearly several considerations when selecting a fluid or its components. Starting with a high-quality base stock is an important first step. The additization of the thermal fluid—with the right combination of antioxidants, yellow metal inhibitors and anti-foam additives—further improves performance to ensure a long lifetime for both the fluid and the electrical components.
Fluids for BEV immersion cooling must be electrically insulating, chemically stable and compatible with all battery materials of construction. In addition, the ideal fluid should suppress combustion in the event of damage to the battery.
The LANXESS portfolio includes different fluid technologies that meet these requirements.
- Polyalphaolefin (PAO) fluids. High purity, chemically inert, synthetic hydrocarbons offer a good combination of thermal and electrical properties while maintaining fluidity at extremely low temperatures.
- Polyol ester (POE) fluids. Based on LANXESS Hatcol® high purity esters, these products provide superior thermal and electrical properties. Some are classified as “less flammable” due to having fire points above 300 °C and many are on the EcoLabel LuSC list.
- Phosphate ester (PE) fluids. Based on the same fire resistant phosphate ester fluid technology as the industry leading LANXESS Reolube® fire resistant hydraulic fluids, PE fluids offer an excellent combination of fire and combustion protection in the event of an accident or electrical failure.
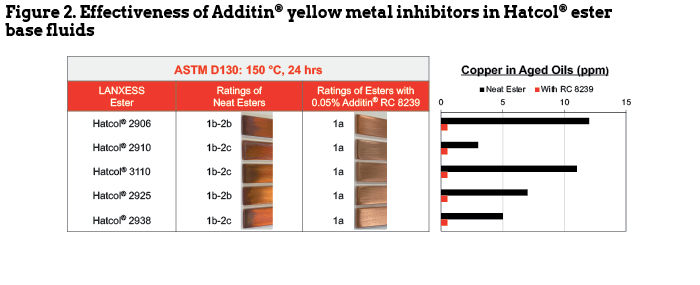
Additives can also enhance performance for immersion cooling applications and offer additional protection.
LANXESS phenolic antioxidants, such as Additin® RC 7115, ensure long fluid life and Additin® triazoles protect copper surfaces (Figure 2). The liquid form of Additin® RC 8239 makes it easy to blend and it is on the EU EcoLabel LuSC list.
Wet E-motor Systems
So called “wet” e-motor designs are already commonplace and use standard automatic transmission fluids (ATFs). However, the expected increase in their uptake in the future will likely require innovative, longer-lasting, fluids that can cope with even more extreme operating conditions and have better thermal stability, heat transfer and electric properties.
Material compatibility is a particular concern with wet designs, as the transmission fluid could potentially come into contact with the copper windings of the e-motor and cause corrosion.
LANXESS has therefore created a new generation of EP additives that are less reactive toward copper and have better stability than current additives.
Hundreds of different tests are carried out at its laboratories and technical centers across the globe to ensure the suitability of these fluids. It has specifically developed three new tests for wet e-drivelines: copper wire insulation (CuWIT), copper wire corrosion (CuWCT) and conductivity of lubricants (COLT).
Figure 3 shows how its two booster packages, E 559 and E 560, compare in terms of EP performance (FZG testing), copper corrosion and temperature stability.

To further enhance the extreme pressure and antiwear performance of existing fluids, LANXESS also offers a “booster package” for automotive lubricants to make them suitable for new BEV applications. The added benefit is that OEMs and lubricant suppliers do not need to spend time and money formulating completely new transmission fluids themselves.
LANXESS’ expansive range of materials and technologies are helping to protect batteries and e-drivelines to ensure they achieve the required levels of performance and the future needs of the automotive industry.
LANXESS is also looking forward to partnering with lubricant blenders and automotive OEMs to create new components and formulations for the next generation of vehicles and these exciting new applications.
For more information, visit https://lanxess.com/en/Products-and-Solutions/Focus-Topics/LANXESS-e-Mobility