Spotlight on Electric Vehicles
Amidst the hubbub surrounding battery electric vehicles, there is a small yet growing conversation about hydrogen-powered transport. When not bonded to carbon to form oil, hydrogen could be a bridge fuel between the need for zero-emissions transport and off-putting battery charging times.
Hydrogen vehicles can be propelled in two ways. A hydrogen fuel cell uses the physics of sub-atomic particles to create an electrical current. Like a BEV, it uses electric motors to drive the wheels. Also like a BEV, it doesn’t require a few liters of engine oil.
A more conventional application is replacing gasoline in internal combustion engine technology with hydrogen. Save for a small amount of incinerated lubricant, a hydrogen ICE produces virtually no carbon emissions.
If the technology takes off, it could be good news for lubricant blenders concerned about the rapid growth of BEVs and approaching bans on ICE and hybrid sales around the world.
Using hydrogen as a combustible vehicle fuel dates back to the 19th Century. In 1860, Belgian-French engineer Etienne Lenoir built a hydrogen-powered carriage called the “hippomobile.” During the siege of Lenningrad, the Soviets converted trucks to run off hydrogen. In 1970, more than a century after Lenoir, inventor Paul Dieges patented a modification that allowed a gasoline engine to run on this most-abundant element in the universe.
Between the 1990s and the 2010s, Ford, Mazda, BMW and even Aston Martin had dabbled with hydrogen ICEs to no avail. But now, Toyota has revealed that by 2025, its iconic Prius will be powered by a hydrogen ICE, according to Japanese automotive media.
Advantages and Disadvantages
Hydrogen technology has some specific challenges. Although not insurmountable, they could be a barrier to greater development at this stage. A hydrogen ICE requires different materials, adjustments to injection and combustion management systems, and reformulated lubricants.
According to the National Hydrogen Alliance, hydrogen ICEs can cost one and a half times more to produce than conventional ICEs. Engines must have hardened valve systems, reinforced connecting rods, specialized spark plugs, higher voltage ignition coils, gas-capable fuel injectors, larger crankshaft dampers, stronger head gaskets, modified intake manifolds, positive pressure superchargers and high-temperature engine oils.
Even though no carbon dioxide is emitted, a hydrogen ICE can produce nitrogen oxides. This toxic gas can either be collected by a catalytic means similar to a diesel engine or by aspirating the fuel far more than gasoline, which in turn reduces power.
This leads to another problem: energy efficiency. About 25% of the energy value of the hydrogen is transferred from production of the gas to powering the wheels. In an FCEV, it is about 30% and a BEV is around 75%, according to Volkswagen.
A further disadvantage is the current lack of infrastructure. But there is a raft of projects on the horizon—especially in Europe—that could change that.
Green Hydrogen Projects
Producing hydrogen from extracted hydrocarbons has a high environmental cost, while producing it from renewable sources by electrolysis is energy intensive.
Annual global investments in green hydrogen are now expected to exceed $1 billion by 2023, and spending will accelerate rapidly thereafter. IHS Markit predicts that from 2020 through 2030, $44 billion will be invested in green and blue hydrogen projects in five European countries alone—France, Germany, Italy, Portugal and Spain.
Europe represents about half of the global planned capacity for electrolysis hydrogen production. The European Union has a target to provide a total of 40 gigawatts of electrolyzer capacity to produce green hydrogen by 2030. As a result, a wave of hydrogen strategies was proposed in 2020.
Germany: AquaVentus involves installation of 10 GW of electrolysis capacity for green hydrogen production from offshore wind power between Heligoland and the Dogger sand bank. The AquaDuctus hydrogen transportation project includes installation of a pipeline from the North Sea to Germany and the rest of continental Europe with capacity of 1 million metric tons per year. It is due for completion in 2035.
Poland: Polish energy company Orlen’s Hydrogen Eagle green hydrogen project will have capacity to produce 50,000 t/y by 2030 from municipal waste. The project also includes six new renewable energy-powered hydrogen hubs in Poland, Czechia and Slovakia, and more than 100 hydrogen refueling stations across the three countries.
Greece: The proposed White Dragon project aims to replace coal with solar power to produce green hydrogen by electrolysis. The gas will be stored and used in fuel cells to generate electricity and heat.
Australia: The Australians have four hydrogen projects on the slate. The Asian Renewable Hub has capacity of 1.75 million t/y and is expected to come on stream before 2028. The HyEnergy Zero Carbon Hydrogen project has expected capacity of 8 million t/y. The Western Green Energy Hub will have capacity of 28 million t/y, and the Murchison Renewable Hydrogen Project will produce 5 million t/y.
Saudi Arabia: ACWA has planned production of 237,250 t/y by 2025 for export.
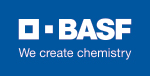
E-mobility Era Requires New Types of Lubrication
The pursuit of better performance and increased efficiencies for electric vehicles is charging the development of ever more innovative lubricants. And BASF, with its extensive portfolio of essential lubricant components, is particularly well positioned to help industry players choose the right components for future e-fluids and to drive e-mobility forward.
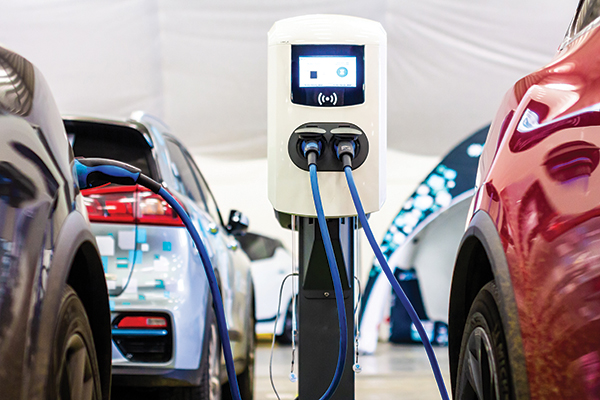
The latest electric cars have many different requirements in terms of lubrication and, as yet, there is still no single preferred technology or fluid concept. The build of an electric vehicle very much depends on the OEM and the model, and as there is no set standard or specification, the fluid requirements are equally diverse.
“For that reason, the industry requires a holistic approach, along with close collaboration, established sustainability expertise and an openness across the value chain,” says Dr. Frank Rittig, technical marketing – Performance Components at BASF’s Fuel and Lubricant Solutions business.
“This is a market with enormous innovation potential and its fair share of challenges across the value chain.”
Over the years, BASF has successfully positioned itself as a leading component supplier for lubricant manufacturers globally to address the specific needs of its customers. A dedicated e-fluids team has been established with a strong focus on customer collaboration that covers a broad range of technologies and capabilities to meet and exceed even the most demanding fluid requirements.
For the motor and gearing in battery electric vehicles, there is a steady trend of moving away from conventional systems with a single gear transmission toward a more compact integrated design, requiring more advanced fluids, i.e. dielectric fluids, to cool and lubricate.
Although the industry has responded by developing smaller and more efficient engines, these tend to generate more heat. While it is therefore not only important to provide the right lubrication, the associated thermal challenges—such as heat conductivity—must also be properly managed, notes Rittig.
Other important properties of modern lubricants and oils for e-mobility applications must include electrical conductivity properties, copper protection and compatibility with varied materials, such as plastics, coatings and the insulating materials of plugs and wires.
Modern engines are under constant strain, particularly given their rapid acceleration and the associated impact on the gears. They have to reliably and safely operate at extreme temperatures, so it is important to select sophisticated oils with very specific properties to ensure a positive and safe driving experience.
Selecting the right chemistries and carefully choosing the additives and base stocks has therefore never been more important—particularly when it comes to the thermal and electrical properties, and the high and still emerging performance requirements.
With electric vehicle demand gathering pace, the lubricant industry is in true need of innovative players to enable the next evolution in technologies for future mobility. “Our significant innovation and sustainability resources, together with our broad portfolio of lubricant components, means BASF is particularly well placed to collaborate with our customers to ensure their success in the future,” concludes Rittig. “We are an international team of engineers and chemists, located in all major regions, with long term experience and in-depth expertise in the lubricant industry, covering many different competencies supported by established global R&D centers. We are passionate about sustainability and strive to offer customized solutions to support the industry in this transformation.”
To find out more about e-mobility and how BASF’s Fuel and Lubricant Solutions business is helping shape the future, visit www.basf.com/future-mobility-fuel-lubes or contact fuel-lubes@basf.com.