Plastic pollution is a serious and constantly growing environmental threat. In 2022, global annual plastics production reached 460 million tons. Estimated global discharge of plastic waste to the environment was 22 million tons in 2019, and this estimate is projected to double by 2060.
Unfortunately, even though plastic waste can be used as a raw material in the chemical industry, there is a lack of systematic collection and sustainable management at the scale needed to fix the environmental issues created by plastic waste. It is estimated that nearly 80% of plastic that ends up in world oceans comes from 2% of the rivers, with the largest portion of river plastic coming from farms, not from metro areas. The four major ocean plastic waste polluters are Philippines, India, Malaysia and China.
The use of plastics in agri-food systems and food value chains is particularly widespread. Examples of plastic products used in modern agriculture include the following:
- Mulch films: to reduce weed growth, evaporative water losses, the need for pesticides, fertilizer and irrigation, whilst also enhancing plant growth
- Tunnel and greenhouse films and nets: to protect and enhance plant growth, extend cropping seasons and increase yields
- Irrigation tubes and driplines: to optimize water use
- Bags and sacks: to transport seeds and fertilizers to nurseries and fields
- Silage films: to aid fermentation of biomass for animal fodder and avoid the need for storage buildings
- Bottles: to transport liquid pesticides and fertilizers to nurseries and fields
- Coatings on fertilizers, pesticides and seeds: to control the rate of release of chemicals or improve germination
- Non-woven protective textiles or “fleece”: to protect crops from extreme cold and/or sunlight
- Fruit protectors: bags, sheaths and nets, sometimes impregnated with pesticides to cover and protect fruit from insect and weather damage
- Plant protectors: to protect young seedlings/saplings against damage by animals and provide a microclimate that enhances growth
- Nets, ropes, lines, traps and enclosures: to catch and farm fish and other aquatic species.
Polyethylene (PE) and polypropylene (PP) are two common polymers used in agriculture for multiple applications. These polymers can be readily upcycled into value-added products. Thermal cracking, or pyrolysis, is one common technique used to convert a wide range of plastics into a complex mixture of alkanes, alkenes, alkynes and aromatics that can be further used in traditional petrochemical processes. The thermal decomposition of PE and PP plastics involves free radical reactions. Both the reaction kinetics and the carbon number distribution in the product depend strongly on the temperature. The typical pyrolysis temperature range is from 400oC to 700oC, with lower temperatures favoring the formation of wax and liquid products (C10-C50), and higher temperatures favoring the formation of gas. Steam cracking at 800oC to 900oC can be used to directly produce ethylene, which is a convenient building block for many other chemistries, such as alpha-olefins and polyalphaolefins. However, high energy demand of high-temperature cracking makes this process uneconomical as far as plastic upcycling is concerned. KATA’s innovative process of Controlled Thermal Chain Scission (CTCS) at temperatures below 400oC delivers a better economy.
Another possibility is catalytic hydrogenolysis, which uses hydrogen to cleave carbon-carbon bonds producing predominantly alkanes. Technologically, processing PE and PP waste plastic in a refinery has many similarities with processing the Fischer-Tropsch (FT) wax (see Figure 1).
Figure 1. Conversion of FT wax to base oils and fuels using hydrocracking and hydroisomerization
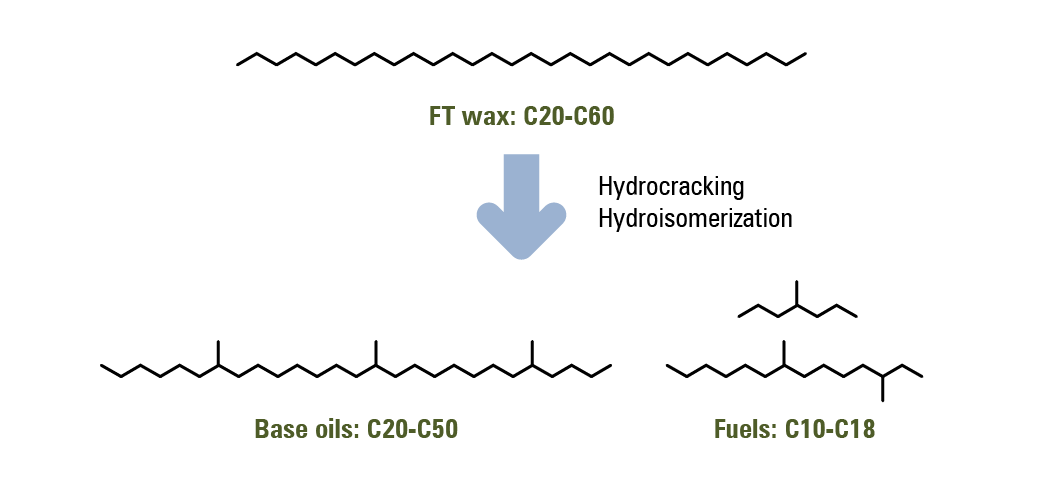
Source for all: KATA
The FT process is the basis for nearly all industrial processes dealing with conversion of natural gas and coal to more valuable liquid hydrocarbons. In the past decades, lubricating oils derived from FT waxes started to gain interest. Unfortunately, the availability of FT waxes is rather limited to cover market needs. In such a situation, waste plastic avails itself as a perfect substitute for FT and slack waxes from petroleum refining, leading the way to a truly sustainable process with a greatly reduced carbon footprint and environmental impact. Instead of dumping waste plastic in landfills, we can convert it into value-added sustainable chemicals.
Unfortunately, so far, these processes have not been economically competitive with traditional crude oil processing. However, the situation is gradually changing thanks to the introduction of carbon credits and an increased push for lifecycle assessment (LCA) and environmental product declaration (EPD).
We at KATA have found a new way to chemically transform agricultural plastic waste at scale using an innovative and energy-efficient, ultralow-emissions and high-throughput process. Figure 2 shows a simplified process flow. The process allows conversion of PE and PP agricultural waste plastic into high-quality, sustainable, multi-purpose fuels, solvents and base oils in a highly cost-efficient way, with the yield of value-added products being close to 80%. The actual partitioning of individual products depends on process conditions; we can prioritize the production of fuel, the production of solvents, the production of base oils, and so on.
Figure 2. Process flow for waste plastic upcycling at KATA
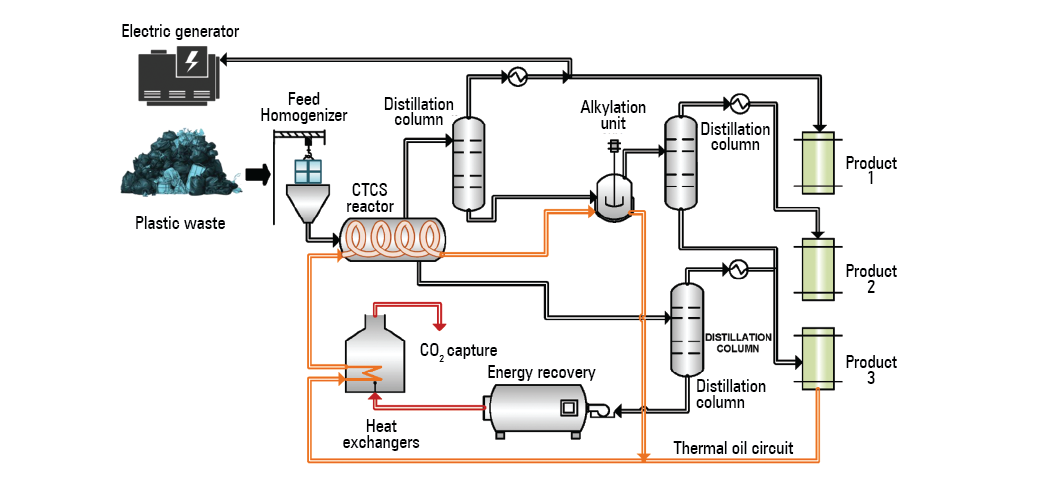
Originating from a non-petroleum feedstock, KATA products contain virtually no aromatic and naphthenic molecules, being largely composed of normal and iso-paraffins. Compared to traditional chemicals from petroleum, KATA products have more narrow molecular weights and boiling points distribution. They combine good low-temperature flow properties and oxidation stability. Lighter fractions (200oC to 300oC boiling point range) can be used to produce sustainable premium diesel. As the chemical composition is concerned, sustainable diesel produced from waste plastic is quite similar to diesel produced using the Fischer-Tropsch synthesis. Both products contain virtually no sulfur, aromatics and naphthenes, and are characterized by a high cetane rating, low cloud and cold filter plugging points, and excellent stability.
Apart from waste plastic upcycling, we collaborate with large sustainable farms to produce a variety of biobased products from such biomass as coconut, castor, and palm oil. The products include ethyl laurate, ethyl ricinoleate and glycerol mono ricinoleate, and can be used as friction modifiers, coolants for electric vehicles, lubricity improvers, co-emulsifiers, solvency improvers, etc., with possible applications in environmentally acceptable marine lubricants, automotive and industrial lubricants, lubricating greases, coatings, cosmetics, pharmaceuticals and more.
Figure 3 shows the MTM test data comparing friction-reducing efficiency of various organic friction modifiers at a 0.5% treat level in PAO4 base oil. GMO and OA are two widely used organic friction modifiers (glycerol monooleate and oleyl amide), and MoDTC is an inorganic friction modifier (molybdenum dithiocarbamate). OFM is our novel biobased polymeric organic friction modifier obtained from castor and rapeseed oil. Being 100% renewable, biodegradable and demonstrating top-of-the-class efficiency and excellent effect retention under oxidative stress, this product is viewed as an attractive alternative to inorganic friction modifiers in industrial and transportation lubricants.
Figure 3. MTM test data comparing the tribological efficiency of various friction modifiers
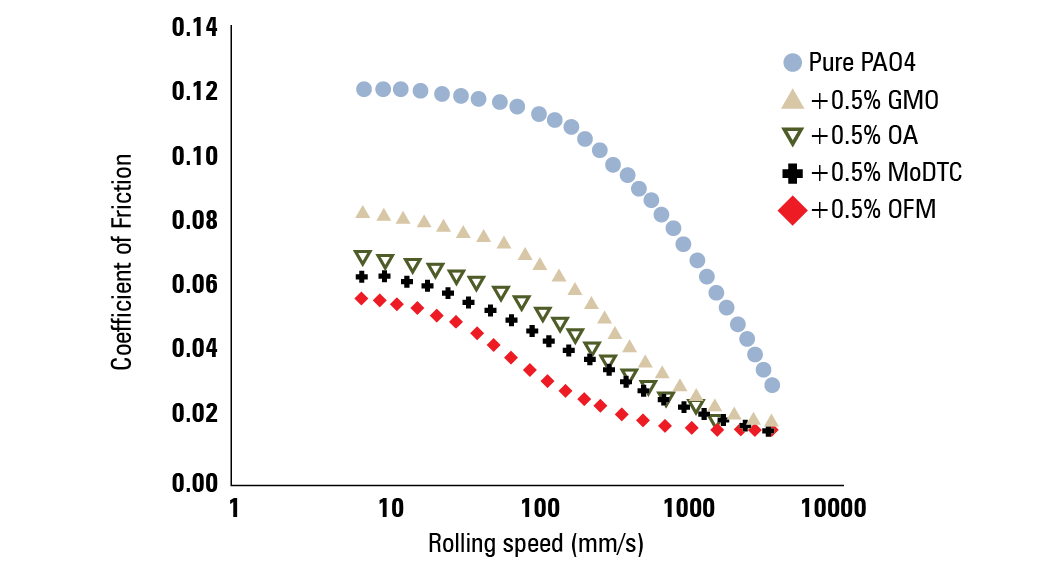
Last but not least, our operations rely upon a closed loop supply chain, leading the way toward a sustainable future. We collect waste plastic from local farmers, convert it to value-added products, such as agricultural lubricants, fuels and crop protection oils, which are then sold back to the farmers. Furthermore, we do this at a scale significant enough to solve the plastic waste problem in the region while bringing benefit to the local farming communities.
Matias de Tezanos, CEO for KATA Circular Pte Ltd, can be reached at mdt@kata.com
Boris Zhmud, TMS Lead at KATA Circular Pte Ltd, can be contacted at bz@kata.com