Before we can truly embrace sustainability, we must understand what it means and how far our businesses are from actually realizing their sustainability goals. Every business activity is accompanied by some type of consumption of materials and energy, and only sustainable consumption provides a chance for true sustainability to become a reality.
Herman E. Daly from the University of Maryland’s School of Public Policy formulated three simple rules to help define the sustainable limits to material and energy throughput. The first rule states that for renewable resources, the sustainable rate of use cannot be higher than the rate of regeneration. The second rule dictates that for non-renewable resources, the sustainable rate of use cannot be higher than the rate at which a renewable resource can be substituted. The third rule says that for pollutants, the sustainable rate of emissions cannot be higher than the rate at which that pollutant can be recycled, absorbed or rendered harmless in its sink.
This, however, is theory. In reality, every production site is under pressure to grow. Year to year, each business must show increasing numbers, especially in regard to profits. This wouldn’t be a bad thing if our planet also grew year to year. But it doesn’t and therefore cannot accommodate careless consumption.
Sustainability is a complex process containing multiple steps, including manufacturing, recycling, reuse and replacement of traditional materials with renewable substitutes (see Figure 1). In my opinion, the only solution to our sustainability woes is to incorporate all the steps mentioned above into our business practices. Only then will we be allowed to say, “We do sustainability.”
Figure 1. Step Toward Sustainability
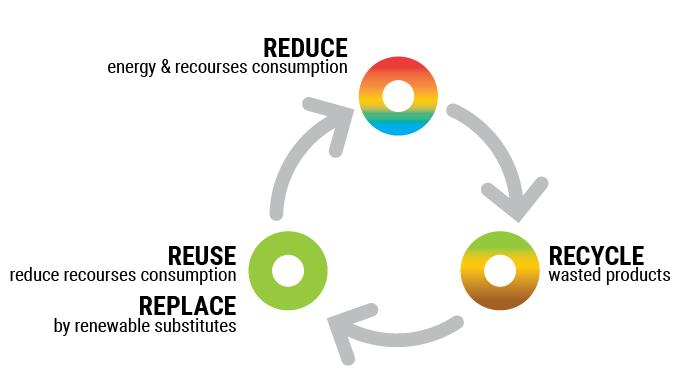
Reimagining Lubricant Blending
So how can rethinking how we blend lubricants help the industry step further onto the path of sustainability?
It is a vital time to act in terms of CO2 emissions reductions. One way that the lubricants industry can do their part is by continuous improvement of the blending process. After all, annual business growth should also include an annual reduction of carbon footprint.
In this article, I will explain how the main blending process—which occurs when all components are in the tank—can be tweaked to achieve bottom limits in time and energy consumption, especially in terms of decarbonization and the reduction of natural environment pollution.
Enter Cold Blending
Let’s talk about your blending installation. Is it similar to the image on the left side of Figure 2 of a traditional installation, or does it look more like the newer, more energy-efficient installation on the right side?
Figure 2. Cold Blending installation (right) replacing an old blender.
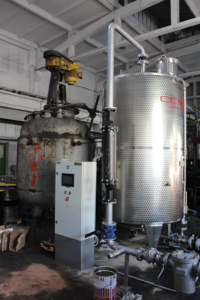
As mentioned above, it is important to reduce the carbon footprint of your manufacturing process, even if the reduction is slight. After all, if we summarize the dispersed effect of energy consumption reduction per all blending plants, the final numbers can add up to be significant in the context of the entire blending sector.
So how can you reduce energy consumption in the main blending process?
In the case of a classic blender with an agitator and heating coils, energy consumption can be reduced by simply decreasing the process temperature. However, this solution comes with a couple of drawbacks: The time that it takes to blend each batch will increase, and the homogenization level will drop.
So what can you do instead?
You can implement a process called Cold Blending that is able to work efficiently at lower temperatures. Cold Blending (CCBL®) technology can give you a reduction of process temperature as well as blending time. Its energy consumption relates directly to the working pump and Automation Control Cabinet.
What about the heating in Cold Blending?
We began by heating the premix, because this energy is necessary for effective and stable sticking of oil macromolecules to additives. Cold Blending changes only the source of energy; instead of slow-heating the entire volume, we ran millions of microheaters inside the oil. Thanks to a fully controlled cavitation process—initiated in the CCBL(R)Jet—we used energy emitted by imploding bubbles. These nanosecond pulses heated up the oil without viscosity destruction and without burning it. Because of this, we were able to reach higher homogenization than in classic blending.
Many of us lubricant blenders are familiar with “Pulsair” technology, which uses air bubbles as a mixing factor. This installation requires compressors, which, of course, consume energy. For fans of this type of technology, CCBL® offers the same kind of mixing, but it is also a free-of-charge mixing component. This is because, as you remember, we initiate sucking of the gas contained in oil by fast-changing the premix stream velocity, which creates millions of bubbles. Part of the bubbles implode, giving heating energy to our blending process, while the other part flow with the stream to the mixing tank. See Figure 3.
Figure 3. Oil saturated with gas bubbles
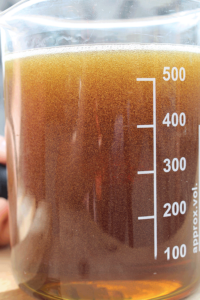
As oil’s viscosity is relatively high, there is no time to release the bubbles into the atmosphere. Only after the blending process has been stopped and is waiting for laboratory results do the bubbles release into the atmosphere. But before leaving the finished lubricant, the bubbles facilitate the final smooth blending, similar to the bubbles created in the “Pulsair” system.
From Your Yard to the Global Market
What can you gain by implementing Cold Blending technology in your lubricants blending plant?
The first—and perhaps most important—benefit of Cold Blending is its ability to reduce your operation’s CO2 emissions, as the CCBL Jet (see Figure 4) can effectively mix any type of lubricating oil at a minimum premix temperature of 23 °C. After all, we no longer live in the stone age, and ecological awareness must increase.
Figure 4. CCBL®Jet, capacity 30 m3/h
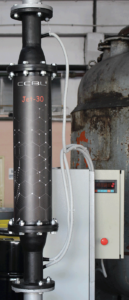
Secondly—and of a similar vein—Cold Blending technology can reduce your company’s consumption of raw materials and energy. Take a look at the following example to understand how this can occur:
I have a client who needs 5 cubic meters of natural gas to produce 1 metric ton of lubricants with classic blending techniques. In 2022, he produced 3,000 metric tons of oils mixed with Cold Blending technology. That year, his usage of natural gas totaled around 15,000 m3 less than it did when he was employing traditional blending processes. Furthermore, the average energy consumption in lubricant blending is around 0.095 megawatt-hours per ton, while Cold Blending technology consumes just 0.0013 MWh/t.
My customer’s emissions were also down significantly. Taking into account that the combustion of 1 m3 of natural gas causes the emission of 1.9 kilograms of CO2, my customer’s emissions were reduced by 25,500.00 kilograms.
Thirdly, Cold Blending technology can actually improve your supply chain, too. By using Cold Blending technology, many blending plants could produce lubricants on a just-in-time basis, where orders are placed before noon, for example, and are delivered by that same afternoon. Better flexibility in production can reduce the volume of unsold batches that are sitting in storage waiting for the day of sale.
So what could be the consequences of such massive reductions in energy consumption in blending plants around the world?
Considering that CO2 emissions are 573 kgCO2-e per 1 megawatt-hour and assuming that about 1% of total refined petroleum products are used to make base oils for lubricant blending, see the results in Table 1.
Table 1. Traditional Lubricant Blending Energy Consumption
Annual | Average Energy Consumption 0.095 MWh/Mt | Emission 573 kg CO2e/MWh | |||||
---|---|---|---|---|---|---|---|
1.00% | daily MWh/t | annual MWh/t | daily (kg) | annual (kg) | |||
United States | 28,742 | 2,730.52 | 996,641.55 | 1,564,590.71 | 571,075,610.97 | ||
European Union | 20,568 | 1,953.98 | 713,203.72 | 1,119,632.14 | 408,665,732.71 |
Now, considering that the Cold Blending process needs 0.0013 kilowatt-hours per metric ton, we could reach the numbers displayed in Table 2.
Table 2. Cold Blending Energy Consumption
Annual | Average Energy Consumption 0.095 MWh/Mt | Emission 573 kg CO2e/MWh | |||||
---|---|---|---|---|---|---|---|
1.00% | daily MWh/t | annual MWh/t | daily (kg) | annual (kg) | |||
United States | 28,742 | 37.37 | 13,638.25 | 21,410.19 | 7,814,718.89 | ||
European Union | 20,568 | 26.74 | 9,759.63 | 15,321.28 | 5,592,267.92 |
Mixing a Quality Lubricant
Of course, it is important to mix lubricants in a sustainable way. But it is also vital for the lubricants being blended to be of the highest possible quality. Because of this, I believe that the certification of oils should be obligatory and that every deviation from quantitative parameters should have severe consequences.
Furthermore, bottom limits should be the same for every lubricant blending plant according to the demands of both qualitative and quantitative indicators. For example, a 5W-40 oil should be 5W-40 exactly, not almost or nearly 5W-40.
Qualitative indicators, which should grow from year to year, include all of the following:
- Minimum emissions of CO2 per 1 metric ton of finished product,
- Minimum % rate of rerefined base oils in the formulation mix
- Minimum % rate of renewable energy in the energy consumption mix
Meanwhile, quantitative indicators should consist of the entire list of parameters from a product’s technical data sheet, with small plus/minus tolerances.
The State of the Cold Blending Endeavor
To some, the reduction of energy and materials consumption to very low levels may seem like a pipe dream, but we may be closer to making this a reality than we realize. So what is the situation in the “blending” garden right now?
Engine oils should allow for 15,000 kilometers between oil changes for passenger cars. This goal has been realized. But it should be ensured that this is the case for older, used cars as well as new ones.
There should be a reduction of energy consumption during the main blending process. This goal has also been realized, but there does appear to be a slight lag in users’ motivation and enthusiasm to implement more energy-efficient processes, such as Cold Blending technology.
There should be a reduction of energy consumption during the process in which viscosity improvers are dissolved in hot oil. This is possible but not completely achieved yet. After the first tests, we have observed positive results. However, we need financial support from investors who are willing to wait a year or two for full commercialization of the project.
Eventually, we should be able to run the entire blending process on renewable energy only. While this is not currently a reality, it is becoming more and more possible thanks to step-by-step energy consumption reductions in the entire blending process.
Conclusions
As you can see, sustainability is not only a button to click on a website or a simple marketing ploy. Instead, there are real activities being conducted right now that will lead to the decarbonization of lubricant blending. And while it is not easy to launch such activities—especially if we can see that other industrial sectors are not thinking about the elimination of low-end products, wasted energy and recourses—it is entirely possible.
Generally, I believe that we are dealing with a stage of overproduction on the one hand and deep poverty on the other. I won’t expand on this topic in this article; however, when Forbes publishes the first list of people who contributed to the implementation of poverty reduction projects and when the reduction of CO2 emissions will be an obvious item on the annual balance sheet of every company, we will then be able to seriously talk about sustainable development.
Andrzej Chodyniecki is the founder and owner of Warsaw, Poland-based GQOIL Innovation.