For a long time, the idea that environmentally acceptable lubricants—commonly referred to as EALs—could not provide comparable levels of performance as traditional lubricant formulations was largely true. But today, EALs formulated with the right chemistries can deliver reliable performance in a broad range of critical industrial applications
Significant volumes of industrial fluids are leaked into the environment through machine seepage, spillages and careless disposal every year. As the world continuously seeks to become more environmentally conscious, minimizing the impact of such losses has become increasingly critical.
New demand for lubricants with environmental protective properties has been driven by regulatory requirements, social responsibility to protect the land and sea, and a general goal to create a clean future for our planet. We have seen the increasing stringency of standards like the European Union’s EcoLabel, which certifies products with a guaranteed, independently verified low environmental impact, and Blue Angel, the German Ecolabel, which the country awards to a wide variety of environmentally friendly products.
In the United States, the Environmental Protection Agency’s Vessel General Permit is being replaced with the Vessel Incidental Discharge Act, which establishes a framework for the regulation of discharges incidental to the normal operation of a vessel under a new Clean Water Act. Biodegradability—the capacity of lubricants to be decomposed by microorganisms over time into simpler byproducts, ultimately carbon dioxide and water—has become a highly desirable trait.
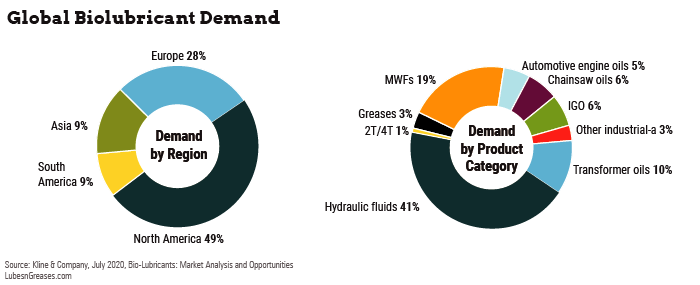
It is within this regulatory environment that we see new growth potential for environmentally acceptable lubricants. EALs are fluid formulations that have been proven to meet such regulatory standards for biodegradability, non-bioaccumulative potential and minimal toxicity to aquatic life compared to conventional lubricants. As widespread regulatory measures have spurred lubricant manufacturers to make their product lines more environmentally friendly, demand for EALs is increasing. Under an optimistic scenario, demand for biolubricant products is forecast to grow at a compound annual growth rate of 5.4%, according to research from Kline & Co.
There is new opportunity for lubricant manufacturers and formulators within the EAL space. But seizing such opportunity is contingent on EAL formulations that can meet, or even exceed, the required performance expectations of conventional fluids. End users and original equipment manufacturers depend on fluids to reliably protect and enable machinery to function as intended. They are not likely to sacrifice such performance for environmental friendliness.
Meeting EAL criteria while delivering high levels of performance is a true formulation challenge. And for much of their history, it was true that EAL formulations could not quite match what was possible with a conventional fluid in terms of protection and performance. But today that has changed. With the right combination of advanced chemistries, EALs have the potential to deliver enhanced performance in a broad range of industrial applications—from hydraulic fluids to industrial gear oils, metalworking fluids and greases.
Defining EALs
EALs, as defined by the U.S. Environmental Protection Agency, have demonstrated acceptable levels of biodegradability, minimal aquatic toxicity and non-bioaccumulative potential. To best understand the formulation challenges associated with them, it is helpful to dive deeper into these definitions:
- Biodegradability: The capacity of lubricants to be decomposed by microorganisms over time into 1) a combination of simpler byproducts (primary biodegradation) and 2) carbon dioxide and water (ultimate biodegradation).
- Minimal aquatic toxicity: Low toxicity to aquatic organisms according to tests defined by the Organization for Economic Cooperation and Development as well as EPA test guidelines.
- Bioaccumultative potential: The buildup of chemicals within the tissues of an organism over time.
Performance and Formulation Considerations in EALs
A top consideration for any industrial fluid, no matter the application, is the protection of equipment. Preventing the premature wear of metal surfaces as they come into contact with each other is a core function of a lubricant—and it is as vital in EAL formulations as it is in any other.
However, there are some fundamental formulation changes that must occur to deliver suitable wear protection in an EAL. For example, one of the most reliable and widely used classes of anti-wear additives is zinc dialkyl dithiophosphate (known as ZDDP)—a chemistry that does not naturally biodegrade as necessitated by EAL classifications. Extremely low levels of ZDDP may be permissible, but those levels are not enough to provide the anti-wear protection that the lubricant must deliver. A nonmetallic anti-wear additive solution is required.
In fact, nearly every critical class of additive chemistry is impacted by EAL restrictions, including the following:
- Extreme pressure additives. Extreme pressure additives are required in demanding applications such as industrial gear oils. One commonly deployed class of such additives are sulfurized olefins. Similar to ZDDP, sulfurized olefins do not meet EAL standards for biodegradability, requiring an alternative solution.
- Demulsifiers and emulsifiers. These additives are required in many industrial fluid formulations to either separate water from the fluid or to incorporate the water within it, depending on the application. Typically, these additives are made up of some form of chemical polymer—a long chain of molecules that may or may not meet biodegradation standards for EAL use.
- Viscosity modifiers. Viscosity modifiers are deployed to manage required fluid thickness for a given application. The viscosity modifiers utilized in industrial applications are also polymers that may or may not break down suitably in the environment.
- Antifoam chemistries. When air becomes entrained within an industrial fluid, foam can result, which may compromise its ability to form a protective film. Care must be taken to select antifoam agents that meet EAL criteria.
- Corrosion and rust inhibitors. Many fluids in industrial applications come into regular contact with water and air at elevated temperatures, making the inclusion of corrosion and rust inhibitors in applicable fluids important. There are a variety of options to consider for conventional fluids, but only a few that are applicable to EAL formulation.
- Friction modifiers. Certain applications require a specifically calibrated amount of friction to enable proper performance. Driveline fluids, for example, require precise friction to allow clutch plates to move without slipping. EAL formulations must be careful in their selection of friction modifiers.
Finally, EAL standards restrict the use of traditional mineral oils due to biodegradability and toxicity concerns. These requirements functionally eliminate Group I, II and III base oils (all of which are mineral-oil based) from EAL formulations. Synthetic base oil formulations from Group IV (polyalphaolefins, or PAOs) and Group V (all other base oil types, including polyalkylene glycols, synthetic esters, phosphate esters and others) are required.
Considering these limitations, it is no wonder that matching the performance of conventional industrial fluids was prohibitively challenging. Fortunately, much ground has been gained in this space in recent years. Consider that it was once thought that industrial gear oil applications were simply too challenging for EALs; specifically, EAL formulations failed to deliver critical micropitting performance that is essential to prevent gear failure. But through extensive testing and chemistry development, Lubrizol has recently developed several finished fluid formulations using biobased synthetic ester base oils that have demonstrated the required micropitting performance for demanding industrial gear oil applications.
The truth is that careful formulation and application of innovative chemistries from the right additives supplier can enable EALs to deliver the necessary performance in today’s most challenging industrial applications. And for lubricant manufacturers seeking a competitive advantage in a changing market place, there is growing incentive to pursue such strategies.
Opportunities for Lubricant Marketers
Legislative incentives are not the only reason that environmental awareness is a growing concern for businesses across most industries. Environmental consciousness is a major and growing concern among buyers at all levels. Consumers increasingly demand to know what goes into products they buy and whether or not those components are safe and healthy for the environment. It is a mindset shift that is opening up new opportunities everywhere.
Within the industrial realm, Kline & Co. anticipates that marine, agriculture, construction, mining and offshore power generation will see significant growth potential for EALs in the coming years. Each represents an area with high potential for lubricating fluids to impact the surrounding environment via leakage or mishandling. Demand is expected to be largest throughout North America and Europe in the coming years as legislative measures continue. Hydraulic fluids are expected to be the dominant application for EAL demand, with a range of other industrial applications making up the rest.
For an industrial lubricant marketer, selecting the right additives partner allows you to enhance your eco-conscious reputation and lead the way with products that have been tested and certified as biodegradable, non-bioaccumulative and minimally toxic to aquatçic life. Further, environmentally certified and performance-validated additive solutions can give you a competitive edge by enabling your business to speed its EAL offerings to market with confidence. Working with the right additives supplier can allow your business to expand its offering of highly valued products, gain a greater share of the market and enter new markets.
Demand for EALs is not likely to decrease in a world increasingly concerned with environmental impact. Reach out to your additives supplier for formulation assistance. After all, it is worth investigating possible solutions today to best meet new demand tomorrow.
Joshua Dickstein has spent the past six years working at Lubrizol in the Industrial Oils group. In his current role as a technology development manager, he is responsible for supporting key business developments in hydraulics, industrial gear oils and turbine oils.