In an era of rapid technological advancements, it’s become abundantly clear that automation is no longer a luxury but a necessity for manufacturing businesses. A key area that stands to significantly benefit from automation is the management of industrial fluid coolants in CNC machines.
These systems play a critical role in maintaining the efficiency, longevity and overall performance of industrial machines. However, their upkeep can be resource-intensive, requiring constant monitoring, adjustment and refilling.
It’s here that fully automated industrial fluid coolant systems are revolutionizing the industry. But why is it crucial for the future of manufacturing companies to make this investment?
Below are a few compelling reasons.
Maximize Operational Efficiency
The CNC machining process depends heavily on coolants for optimal performance. Coolants not only keep the machines from overheating but also clear away metal chips and prolong the lifespan of the tooling. However, maintaining optimal coolant levels and concentrations is a challenge, one that can affect the overall machine operation and result in unnecessary wear and tear on expensive tooling. Fully automated coolant systems are a game-changer, driving significant improvements in operational efficiency by optimizing machine operations.
In the absence of a fully automated system, maintaining the optimal coolant levels and concentrations can be a manual, labor-intensive process that’s prone to inconsistencies. However, a fully automated coolant system takes the guesswork out of it.
By maintaining precise coolant concentrations and levels, it ensures that CNC machines are always operating under optimal conditions. This consistency is crucial, as variations in coolant concentration can cause fluctuations in machine performance, affecting both the quality of the output and the overall efficiency of the operation.
A fully automated system significantly reduces wear and tear on CNC machines. Coolant serves as a lubricant and a heat dissipator, ensuring that machines don’t overheat or sustain damage due to friction. With an automated system, you can expect that the coolant is always at the right concentration and level, offering consistent protection to machines. This protection reduces unplanned downtime for maintenance and extends the life of equipment, translating into considerable cost savings in the long term.
Alleviate Staffing Challenges
One of the most pressing issues in today’s manufacturing landscape is the significant shortage of skilled labor. Many factories and shops are grappling with the challenge of maintaining operational efficiency despite these workforce shortages. Here, fully automated coolant systems enable businesses to streamline their operations while empowering their employees to focus on more value-adding tasks.
The aging workforce, shifting demographics and the rapid advancement of technology have all contributed to a severe shortage of skilled labor in the manufacturing sector. This shortage isn’t just a minor inconvenience; it can have significant impacts on a company’s productivity, efficiency and its ability to meet client deadlines.
In a conventional setup, employees would need to monitor and adjust coolant levels and concentrations manually—a time-consuming process that is not only prone to human error but also detracts from more critical tasks. With automation, businesses can reassign these workers to roles that directly contribute to production and efficiency, addressing labor shortages in a meaningful way.
This reallocation of workers to more skilled roles has several benefits. First, it allows workers to apply their skills where they matter most, leading to increased job satisfaction and productivity.
Additionally, by focusing on roles that directly contribute to production, employees can have a more significant impact on the company’s bottom line. This can result in higher output, improved quality and ultimately increased profitability.
Having more hands on deck in critical areas of the production process can boost operational efficiency and reduce lead times, ensuring that your company can meet market demands even amidst labor shortages.
As automation takes over routine tasks, workers can upskill and adapt to more complex roles. This provides a career progression path for employees and ensures that the manufacturing sector can evolve and adapt to changing market conditions and technological advancements.
Cost Savings
The consideration of cost is central to every business decision, especially when it comes to investment in technological advancements. While the upfront cost of implementing such systems may seem substantial, it is important to view this as an investment rather than an expense. Over time, these automated systems can result in significant savings, contributing to operational efficiency and profitability.
One area where savings become immediately apparent is in the reduction of coolant and CNC tooling costs. Automated systems like the Dazzle 2 by Zebra Skimmers can save up to 80% on coolant costs. This is achieved through precise coolant management, where the system maintains optimal concentration and minimizes waste. Over time, the savings on coolant expenses alone can contribute significantly to offsetting the initial investment.
These systems can result in up to 85% savings on CNC tooling expenses. Consistent coolant concentration and levels maintained by the system reduce maintenance needs, prevent tool wear and increase tool lifespan, reducing the need for frequent tool replacements and saving businesses time and money.
Consistent, optimal coolant concentrations and levels ensure that CNC machines operate at their best. This enhanced performance translates into faster, more efficient production cycles and higher-quality output.
Consistency and Quality Assurance
Coolant plays an essential role in the machining process, keeping tools at optimum temperatures, reducing friction and washing away metal chips. However, the manual handling of coolants can often lead to inconsistencies that can negatively affect machine performance and the quality of the product.
In a manual system, operators are responsible for checking and adjusting coolant levels and concentrations. This process can be fraught with potential issues. For instance, each operator may have a slightly different interpretation of the “correct” coolant concentration. Inconsistent measuring techniques or infrequent checks can also lead to variations.
Moreover, manually topping up coolant levels can result in coolant concentration becoming too diluted over time, affecting its effectiveness. Alternatively, if the coolant becomes too concentrated, it can lead to tool wear or damage, affecting the quality and precision of machining operations.
Even when using a Venturi mixer, fluids above 500 SUS still can have problems properly mixing. Fully automated systems overcome these challenges by maintaining those precise coolant concentrations and levels, always ensuring optimal machine conditions.
Zebra Skimmers’ Dazzle 2 system employs a precision mixing algorithm that automatically mixes neat coolant and water to the precise target make-up concentration for each machine sump. Once the concentration and sump high and low levels are set, the system continuously monitors and adjusts the coolant as needed, ensuring the ideal balance is maintained without any human intervention.

The system even uses a self-cleaning process refractometer to continuously monitor the coolant concentration in sumps under management. This feature eliminates the variability that comes with manual readings, resulting in an accurate and consistent coolant mix.
By maintaining ideal coolant levels and concentrations, fully automated systems ensure that CNC machines operate at their best. The consistent cooling and lubrication provided by the precisely mixed coolant ensure that the tools work optimally, leading to higher precision and fewer errors. The net result is a consistent, high-quality output that isn’t subject to the variability inherent in manual coolant management. For any manufacturing business looking to enhance their product quality and operational efficiency, embracing the benefits of coolant automation should be a top priority.
Data Monitoring and Analysis
In today’s Industry 4.0 era, data is the lifeblood that fuels smart decision making and operational efficiency. Modern automated coolant systems leverage sophisticated data collection and analysis tools to bring transformative insights to manufacturing operations.
Here are some features to look for when researching your options:
- Real-Time System Performance Insights. Automated coolant systems continuously monitor crucial parameters like coolant levels, BRIX concentrations and system performance. This real-time data capture enables immediate adjustments. The power of such timely interventions cannot be understated; it maintains the ideal working conditions for your CNC machines, which directly contributes to maximizing output quality and minimizing wear on machinery.
- Identification of Trends. With the capability to capture and store data over extended periods, automated coolant systems offer a macroscopic view of operations. This accumulated data is ripe for analysis, allowing discernment of emerging trends and patterns in coolant usage and machine performance. Identifying these trends aids in strategic decision making—from tweaking daily operations to
informing procurement schedules and even driving R&D efforts for process improvement. - BRIX Level and Coolant Usage Monitoring. Monitoring the BRIX level—a measure of coolant concentration—is a critical aspect of coolant management. Fully automated systems precisely track these levels, alerting operators when adjustments are needed. Similarly, coolant usage can be closely monitored, helping businesses understand their coolant consumption patterns. This aids in efficient inventory management, ensuring that companies always have the necessary supplies on hand without overstocking. Some systems can even alert coolant distributors when supply is getting low.
Data-driven insights provided by automated coolant systems are pivotal in optimizing manufacturing operations. By making sense of this information, businesses can make informed decisions that not only enhance daily operations but also guide strategic planning.
In this way, an investment in a fully automated coolant system is an investment in data-rich, efficient and future-ready operations.
Safety Compliance
A fully automated coolant system mitigates several safety hazards associated with manual coolant management. For instance, direct contact with coolants can pose health risks to workers, including skin and eye irritation or serious conditions upon prolonged exposure.
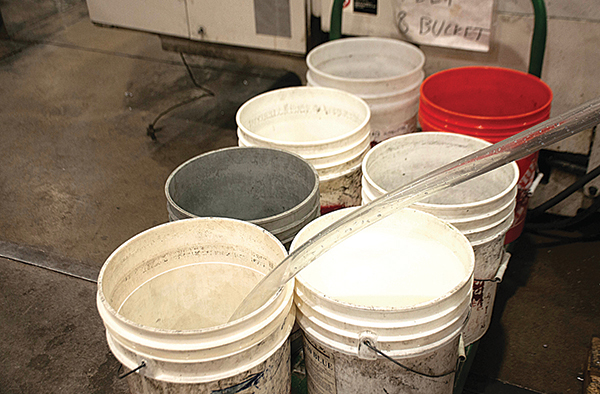
By automating coolant management, such direct contact is significantly reduced. It also eliminates the physical strains related to manual handling of coolant drums, creating an even safer work environment.
Safety isn’t just a legal obligation—it’s a critical determinant of your workers’ morale, productivity and, by extension, the overall operational efficiency of a company.
Ensuring Environmental Compliance
Automated coolant systems precisely control coolant levels and concentrations, using no more coolant than necessary to reduce waste.
Beyond compliance, proactively pursuing environmentally friendly practices reflects positively on your company’s brand image and can confer a competitive advantage in the eyes of increasingly eco-conscious customers.
By enhancing safety and ensuring compliance, a fully automated coolant system is a testament to your commitment to your team members’ wellbeing, environmental stewardship and sustainable success. In this light, the decision to adopt such a system becomes an easy one.
What Does All This Mean?
The value of a fully automated industrial fluid system in a manufacturing environment cannot be overstated. By maintaining optimal coolant levels and concentrations, reducing machine wear and tear, and driving operational efficiency through resource reallocation, these systems play a crucial role in enhancing machine performance, extending equipment life and improving overall business productivity. They are in every sense an investment in the future success of a company.
In an era where manufacturing excellence is synonymous with technological innovation, investing in an automated system is a forward-looking decision. Automation of coolant management not only offers immediate operational benefits but also positions companies for sustainable success in a competitive landscape. By making this investment, manufacturing companies are not merely buying a system—they’re investing in their future.
As we move forward in the era of Industry 4.0 and beyond, embracing such innovation will be key to remaining competitive and driving growth.
Vicky DiMichele is the digital media coordinator for Zebra Skimmers Corp.