The annual cost of corrosion worldwide is about $2.2 trillion, or more than 3% of the world’s GDP, according to the World Corrosion Organization, a nongovernmental organization of the United Nations. This is double the percentage impact due to friction reported by Peter Jost, commonly referred to as the founder of tribology, in his seminal 1960s report on the costs to the British economy of poor lubrication and maintenance.
Lubricants prevent greater losses, although their impact goes un-noticed by many end users. In many lubricant applications, corrosion control is a “table stake” activity where a simple specification can be easily passed with a small amount of generic chemistry. Sometimes corrosion control is a consequential effect of formulating with surface-active ingredients that have a different primary purpose. However, there are other applications where corrosion prevention is the differentiating factor between fluids, and many lubricant companies have specialized corrosion preventive fluids in their portfolios.
Keeping It Simple
While the term corrosion can be applied to the oxidative degradation of ceramics or polymers, this article is about corrosion of the alloys of iron or aluminium that are manufactured and shaped into parts used in lubricated equipment. There’s also a detour into the corrosion of copper and the so-called “yellow metals.”
Corrosion requires water and oxygen to be present at a metal surface. It can be chemical or electrochemical and can take place under either acidic or basic conditions. To prevent corrosion, either the oxygen or the water must be kept away from the surface. Acids can both catalyze oxidation and prevent it.
At the simplest level—during storage or transport, for example—corrosion control can be achieved by use of an oil film to slow the migration of water and oxygen to the metal surfaces. However, water and oxygen are sufficiently soluble in hydrocarbons that garden tools dipped in oil for the winter need to be sharpened in the spring. Their dullness is the result of some limited corrosion over the intervening months.
Crankcase Lubricants
Corrosion due to ambient conditions has almost never been an issue in automotive crankcase lubricants for passenger cars, buses and trucks. This is mainly due to the high treat rates of detergents, said Phil Reeve of Wantage, United Kingdom-based ADLU Consultancy. These calcium- or magnesium-based soaps bear a chemical resemblance to many of the metal-containing corrosion inhibitors added to many industrial lubricants.
“The Sequence IID and IIE were early rust tests, which were passed with sufficient reserve total base number from the detergent,” Reeve told Lubes’n’Greases. “The Sequence II rust tests were replaced by the Ball Rust Test, or BRT, a bench test that many thought to be less severe.” Possibly as a result “some OEMs added a rusting test (usually a bench test) to their specifications for crankcase factory fill oils.” As it may be several months between manufacture and first use, the engine must be protected when the vehicle is stored in the open air or transported long distances by rail, road or sea.
Cylinder Lubricants
Sometimes changed operating conditions can induce corrosion. This became apparent in large low-speed two-stroke marine engines, following the financial crisis of 2008, when cold corrosion appeared on the cylinder liners after ship operators adopted “slow steaming.”
Cold corrosion is caused by condensation of sulfuric acid on the cylinder liners—a consequence of operating vessel engines at lower than optimal loads, leading to cooler cylinder liners than the design operating conditions. Sulfuric acid, formed from combustion, can be related to the sulfur content of the fuel. Traditional 70BN cylinder lubricants were not always capable of neutralizing the acid.
Ian Bown, technical manager – marine engine oils at Lubrizol, told Lubes’n’Greases: “Left unattended, corrosive wear occurs. The rate of material loss can be very high, much higher than the sum of the individual contribution of wear and corrosion. This is because loose corrosion products are easily removed by wear to continually reveal fresh metal beneath, which in turn can corrode quickly. It is likely that high wear rates will be observed with piston rings and cylinder liners requiring more frequent replacement.”
Additive and lubricant companies responded by producing 100BN and 140BN cylinder oils containing additional detergent chemistry to neutralize the acids. Those detergents are usually overbased calcium phenates, sulfonates, salicylates or carboxylates. “Although the global marine fuel sulfur cap has reduced to 0.5% (very low-sulfur fuel oil), cold corrosion still needs to be considered when developing new cylinder oils,” Bown said.
Salt Water
Salt water and its vapors are an issue for any seagoing vessel, as they can induce corrosion. This is a common issue for the greases and lubricants used in on-deck equipment or to lubricate bearings and hinges below the waterline.
Resistance to water washout is the primary concern for greases below the waterline, so aluminum- or calcium-based thickeners are often preferred over lithium analogs due to their generally superior resistance to water. This relationship is also generally true of the corresponding metal complex thickeners. The demands of many grease applications mean that some corrosion-inhibiting additives are almost unique to greases. These include barium sulfonates (natural and synthetic) and bismuth, lead or zinc naphthenates. Others, like sodium sulfonates, fatty amines and amides, imidazolines, benzotriazoles, phosphates or amine phosphates, might also be found in industrial or crankcase lubricants or metalworking fluids.
Industrial Lubricants
Formulators of industrial lubricants usually must pay more attention to corrosion than their crankcase colleagues, as additives treat rates are much lower and the types of surfactants that are used in crankcase lubricants as detergents are usually not present.
Rafe Britton of Lubrication Expert in Sydney, Australia, explained some of the issues: “Water is such a pervasive oil contaminant … and the nature of ingress differs by industry and application. The construction and food industries often suffer from overaggressive washdowns, the chemical and process industries may produce water, while power generation typically deals with environmental contamination—think steam in steam turbines, sea spray in offshore wind, and hygroscopic polyol esters removing moisture from the air in land-based aeroderivative turbines.”
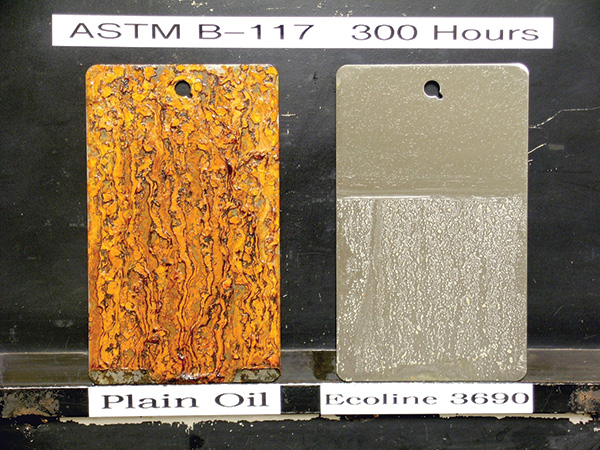
Several strategies are used to combat corrosion. “In the formulation, the protection of ferrous surfaces is typically performed by mildly acidic additives which sit on metal surfaces like seaweed on an ocean floor, excluding water molecules from interacting,” Britton said. “The other means of defense is water separability—this is why most of the wind turbine gear oils are fully PAO-based lubricants and why demulsibility is such an important performance parameter in steam turbine oils. But there is also an increasing focus on excluding water by means of installing desiccant breathers and dry air/nitrogen blanketing systems on reservoirs.”
In the cases above, the metals are mainly steel alloys. Specific corrosion inhibitors may be added to lubricants where corrosion of yellow metals or copper must be prevented. Screw compressors, for example, contain brass, which is often protected by use of a triazole additive.
Working with Water-based Fluids
When steel or aluminum are cast, forged or rolled, corrosion of the formed part, the die or the roller can be a significant issue. Every stage of the value chain—from furnace to finished piece—exposes the surfaces to different temperatures and pressures. The chemistry of the steel or aluminum is modified at each stage, depending on the final application. Often a piece is stored or transported between each stage of manufacture, so the surfaces must be protected from corrosion while awaiting the next stage. This leads to a proliferation of fluids, as each one must be tailored to the metallurgy, form and application.
Graham Twiddle of LUBRO-LOGIC, based in Wolverhampton, U.K., outlined some of the issues faced by fluid formulators for machining applications. “Corrosion in steel is usually initiated by acids, whereas corrosion of aluminium is usually initiated by highly alkaline (basic) solutions. So, if you are machining an aluminium piece using steel tools, your fluid must remain in a very tight window of pH to avoid corroding the tool steel or staining the aluminium workpiece.”

Many different machining operations can be applied to individual workpieces, whether consecutively on one piece of equipment or via several machines connected to a central supply system. The system for aluminium machining usually contains oil, water and entrained air—excellent sources of food for bacteria, which can produce corrosive metabolites. It also introduces the possibility of galvanic corrosion, where electrochemical reduction on the surface of swarf or fines of one metal are coupled with oxidation of the workpiece or tool.
Regulations, like REACH and the Biocidal Product Regulations, have effectively removed many bactericides from the formulator’s palette in Europe and North America. This also impinges on amine borate corrosion inhibitors. On the positive side, they also inhibit bacterial growth, opening the possibility of wider use. However, for about 20 years there has been much uncertainty on how the EU would classify boric acid and its compounds.
(Boric acid is a Substance of Very High Concern under REACH. The issue for many years was whether boric acid in amine borates and related materials could be quantified and whether the amine borates were themselves reprotoxic. The classification of boric acid changes in December 2022, and the Union of the European Lubricants Industry will soon publish a paper explaining the new classification as “CMR 1B”—CMR substances are those that are carcinogenic, mutagenic or toxic to reproduction—and the impact on MWFs.)
Secondary amines, like diethanolamine, provide excellent corrosion control, are basic and have good pH stability. However, they have been replaced due to concerns that they could react with nitrates or nitrites and other nitrogen-based compounds to form nitrosamines that could be carcinogenic.
“During machining operations like drilling, milling, etc., the protective layer of metals is constantly removed,
and a highly reactive fresh metal surface is exposed. Corrosion inhibitors in the MWF passivate these surfaces. They attach temporarily to the metal surfaces and shield it against the corrosive environment.”
– Daniel Griebe, Metall-Chemie |
Acidic corrosion preventives include mono-, di- and tricarboxylic acids, which are well-established corrosion inhibitors for MWF used in ferrous metal machining processes. “The number and orientation of the carboxylic acid groups and the nature of the rest of the molecule determine the corrosion inhibitor performance, foaming behavior, hardwater compatibility and their solubility,” said Daniel Griebe, head of R&D at Hamburg, Germany-based Metall-Chemie. “During machining operations like drilling, milling, etc., the protective layer of metals is constantly removed, and a highly reactive fresh metal surface is exposed. Corrosion inhibitors in the MWF passivate these surfaces. They attach temporarily to the metal surfaces and shield it against the corrosive environment.”
One benefit seized by many marketers recently is the high sustainability credentials of their remaining corrosion inhibitors, as many have been derived from natural products for years.
Cleaning Up
Since MWFs and cleaners for steels are usually alkaline, the corrosion inhibitors can be used in both applications. However, Griebe advised: “The requirements can differ, since cleaners are used prior to final process steps like finishing paint. Therefore, they need to be easily rinseable and almost residue free for proper paint adhesion.”
Lubricants play many roles in protecting against corrosion of the equipment or parts they are used to protect. This can be by binding to surfaces to prevent reactions, neutralizing reactive species or providing the correct chemical conditions for the effective removal of water. Although legislation has reduced formulators’ options, many corrosion inhibitors derived from natural products have received a new level of attractiveness due to interest in sustainability. Steel and aluminum use will continue in all “net zero” scenarios beyond 2050, so there is still a lot of that $2.2 trillion market to aim for. Watch out for many new developments.
Trevor Gauntlett has more than 25 years’ experience in blue chip chemicals and oil companies, including 18 years as the technical expert on Shell’s Lubricants Additives procurement team. He can be contacted at trevor@gauntlettconsulting.co.uk