A Welcome Addition
Additives are a vital component in modern lubricants,
helping to ensure formulations meet strict performance standards while prolonging the lifetime of equipment.
Although additive demand is typically robust and relatively stable, these past few years have contributed a long list of factors that have affected production and dented supply. Only fairly recently have there been signs of volumes rallying, consumption rebounding and a return to normality.
The onset of the COVID-19 pandemic—with its associated lockdowns, travel restrictions and supply chain issues—have all taken their toll. This perfect storm saw additives production drop significantly in 2020 through early 2021.
“COVID-19 and the lockdowns meant fewer people were travelling. They were delaying servicing, and car production plants were shutting down for lengthy periods because of component shortages. That all reduced demand for factory fill engine oil and transmission oil,” said Philip Reeve, director of United Kingdom-based ADLU Consulting. “We saw probably a 5% drop in sales volumes for that period versus pre-COVID-19 levels in terms of additives, although this should pick up this year as economies now open up once again.”
Another contributory factor to the drop in demand, Reeve suggested, were changes seen in the marine additives segment. Volumes declined quite significantly when the International Maritime Organization introduced further restrictions in terms of sulfur limits in fuel and allowable emissions in international waters. With ships subsequently converting to low-sulfur fuels, far less detergent was needed in the formulations, he explained.
There was also a period in 2020 that saw crude oil in the United States enter negative pricing for the first time in history. Weak refinery economics forced shutdowns, which affected base oil production and therefore impacted additives as well.
All these issues were compounded by the so-called big freeze in Texas during February 2021, when unusually cold conditions forced the closure of production facilities on the U.S. Gulf Coast and disrupted supply. What’s more, just weeks later, the blockage of the Suez Canal by one of the world’s largest container ships halted shipments in and out of Asia.
Turnarounds and unexpected outages at various chemical plants were also contributing to a shortage of key raw materials and thereby affecting additives production.
Essential Ingredients
Additives are needed to perform specific functions in a lubricant. Simply put, their purpose is to enhance, prevent and protect—optimizing performance without being detrimental to the core properties of the base oil. Careful selection and compatibility with other additives and the base oil itself is key, so as not to lessen existing attributes.
“Without these important additives and attributes, the base oil just wouldn’t last as long or be as effective,” Reeve said. “The additives perform a valuable function that the base oil characteristics inherently can’t provide.”
According to figures from consultancy Kline & Co, global annual demand for lubricant additives totaled around 4.5 million tons in 2019, including both active component and diluent oil. Automotive remains by far the biggest segment of the market—representing around 60%. The majority is used in the production of heavy-duty and passenger car engine oils to improve fuel economy, increase service intervals and lower harmful emissions.
Depending on the application, the amount of additives included in the finished lubricant varies considerably but can constitute up to a quarter of an automotive engine oil or as much as 40% of a metalworking fluid.
There are numerous classes available, including detergents, dispersants, antioxidants, anti-foaming agents, demulsifiers, emulsifiers, anti-rust agents, pour point depressants, viscosity modifiers and friction modifiers.
Additives vary considerably in form and function and boast many different properties and attributes. They may be required to protect metal surfaces or neutralize acids formed during the combustion process. They are also used for cleaning, inhibiting wear, preventing or encouraging thickening, as well as ensuring more effective operation at different temperatures.
Steering Innovation
The increased focus on sustainability and the push toward greater levels of efficiency—particularly in the automotive sector—are encouraging innovation among additives producers.
Stricter emissions legislation is certainly driving more interest in fuel economy and lower-viscosity oils, Reeve said. There is greater interest in friction modifiers, for example, as producers focus on making engines even more efficient and improving fuel economy.
Hybrid engines are becoming commonplace and by combining a combustion engine and a battery, they may be subject to long periods of inactivity, which can cause corrosion or water ingress. Additives development will inevitably provide new solutions for dealing with these different engine types and conditions.
Nevertheless, bold new breakthroughs with additives tend to be few and far between nowadays, with formulae instead only seeing minor adjustments and enhancements, Reeve said.
“There are some quite significant obstacles to innovation and launching new products. That’s why we tend to see incremental improvements on things that already exist. This is quite an established industry, and if there was
anything that was really revolutionary, somebody
probably would have found it by now.”
– PHILIP REEVE, ADLU CONSULTING |
“In many ways, I don’t think there’s a great appetite for innovation because the hurdles to get something new into the market are now so high,” he explained. “Testing costs, regulatory and HSE hurdles mean registration in some countries can take several years, by which time things may have moved on and there might be different solutions to the problem you started with.”
He continued: “There are some quite significant obstacles to innovation and launching new products. That’s why we tend to see incremental improvements on things that already exist. This is quite an established industry, and if there was anything that was really revolutionary, somebody probably would have found it by now.”
Today, pretty much every lubricant contains an additive in some form, and for the foreseeable future at least, they will continue to play a vital role. Yet with more electrification and the phasing out of the internal combustion engine, fewer additives will be required and demand will shrink.
“That means there’s probably going to be greater competitive pressure on the core market that’s left, and it’s going to be a case of who can control their costs most effectively,” Reeve said. “There will always be a market and need for additives, but it will require a rethink by some producers about how they adapt to the changing times.”
In this Spotlight, LANXESS explains how its sulfur carriers combine versatility and exceptional performance.
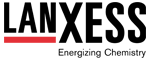
Sulfur Carriers: The “Swiss Knife” for Metalworking Fluids
The most commonly used Extreme Pressure (EP) additives in metalworking applications are sulfur carriers – a generic term for sulfurized natural or synthetic esters or olefins. Germany-based producer LANXESS is one of the world’s largest manufacturers of sulfur carriers, which it sells under the brand name Additin®.
Additin® sulfur carriers are extremely versatile and are ideal for reducing friction and preventing adhesive and abrasive wear in boundary lubrication. The choice of sulfur carriers can be adapted to the specific requirements of different metalworking processes by varying properties like:
- Total sulfur content
- Active to inactive sulfur ratio
- Lubricity
- Polarity
- Solubility
- Corrosion to copper and yellow metals
- Biodegradability
- Viscosity
- Flash point/volatility
- Pour point
Those properties could be influenced by selection of raw materials and process parameters during sulfurization and after treatment (Figure 1).
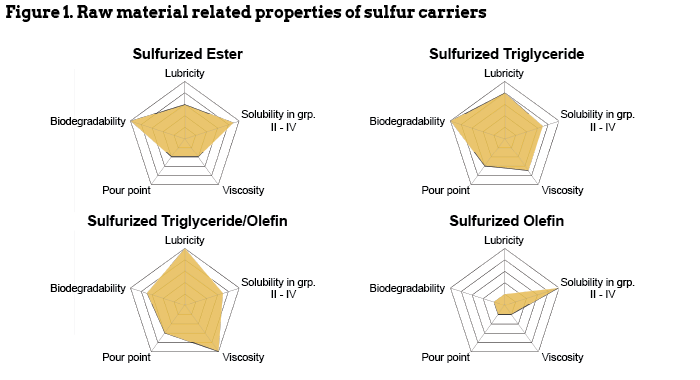
Since the solubility of many conventional sulfur carriers in low polar base oils is quite poor, the shrinking volume of Group I mineral oil and growth of less polar Group II–IV base oils limits the choice of EP additives in modern metalworking oils. Two of the most common types of sulfur carriers for metalworking oils and greases are sulfurized triglycerides and sulfurized triglyceride-olefin reaction products. LANXESS succeeded in adapting their chemical structures, making Additin® RC 2416 and Additin® RC 2516 perfectly soluble in low polar base oils without affecting performance.
The fast generation of fresh metal surfaces in metal cutting and shearing processes requires highly active sulfur carriers – although these tend to stain and even corrode copper and its alloys. Special manufacturing processes allow LANXESS to offer Additin® RC 2541 and Additin® RC 2542, active sulfur carriers with a sulfur content of approximately 40%, which do not stain yellow metals at temperatures up to 100°C.
Chlorinated paraffins (CLPs) are also commonly known EP additives. Short-chain chlorinated paraffins (chain-length C10 – C13) were already banned and eliminated from metalworking fluid formulations in most regions around the world due to their high environmental and human toxicity. Medium-chain chlorinated paraffins (chain-length C14 – C17) are supposed to be banned as well in many countries because of their risks to the ecosystem and to human health. There were discussions in the U.S. about medium-chain and long-chain chlorinated paraffins as well, and these discussions seem to be ongoing.
Chlorinated paraffins (CLPs) work well as EP additives in low-speed metalworking processes. However, with increased machining speeds that also result in higher temperatures of workpiece and tool surfaces, CLPs tend to decompose and form hydrogen chloride, which causes tremendous chemical wear. Additin® sulfur carriers are ideal replacements and even outperform CLPs in most applications.
A field test on a milling machine highlights the deficiencies of CLPs (Figure 2). A milling oil containing 15% of medium-chain chlorinated paraffin (MCCP) showed significantly reduced tool life with increasing machining speed. The tool life declined from 3.5 meters cutting path at a cutting speed of 28 meters per minute to only 1.18 meters at 55 meters per minute cutting speed (indicated by the red bars). This reduction of tool life is caused by the decomposition of the MCCP, followed by corrosion of the milling tool. The chlorinated paraffin containing cutting oil was significantly outperformed by only 5% of the special sulfurized EP additive based on hydrocarbon and triglyceride Additin® RC 2526 (grey bars). At 28 m/min cutting speed, 1% antiwear additive Additin® RC 3760 were added to exceed the performance of the MCCP containing cutting oil (black bars). At higher cutting speeds, Additin® RC 2526 becomes very efficient and clearly outperforms the chlorinated paraffin, even without the addition of other additives.
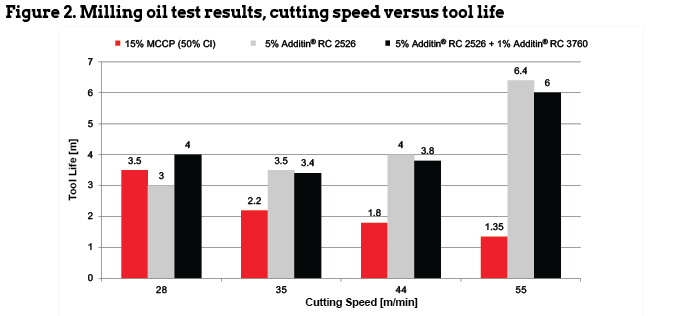
As the electric vehicle market continues to gain traction, there will be an increased demand for forming, stamping, thread forming and fine blanking operations to produce rotor and stator sheets or cases for electric motors and gearboxes. The high surface pressures of stamping and fine blanking processes require EP additives that can effectively prevent adhesive wear. LANXESS Additin® RC 8000, a polymeric sulfur carrier, is able to form extremely pressure stable, friction-reducing protective layers and meets both these requirements.
In a “Press-In test,” which is used to simulate fine blanking, it was possible to reduce adhesion and friction force by approximately 30% with a combination of Additin® RC 8000 and the LANXESS AW additive Additin® RC 3880 when compared to a forming oil containing 40% of chlorinated paraffin (Figure 3).

The EP performance of Additin® sulfur carriers can even be enhanced by synergistic combinations with other additives, including overbased alkaline earth sulfonates, polycarboxylates and esters.
For example, the synergistic effect resulted in friction reduction in thread forming stainless steel. While there is already a significant reduction of friction when replacing 10% chlorinated paraffin by 10% sulfurized olefin Additin® RC 2540, further reduction is possible by synergistically combining Additin® RC 2540 with overbased calcium sulfonate Calcinate®C-400CLR (Figure 4).
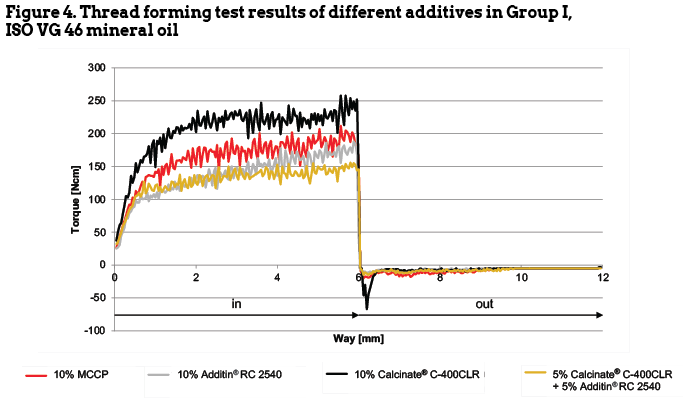
LANXESS Additin® sulfur carriers boast high versatility and superior performance, and meet the requirements of the many different metalworking processes. Several LANXESS sulfur carriers also fulfil the EU criteria for biodegradability and low ecological toxicity and can be used for the formulation of lubricants that meet the requirements of the European Ecolabel and the U.S. Vessel General Permit.
For more information, visit https://lanxess.com/en/Company/Corporate-Structure/Business-Units/Lubricant-Additives-Business