From those serving the largest metropolitan areas to rural communities that are only red dots on a map, municipal wastewater treatment facilities ensure that household sewage, stormwater and some industrial wastewater can be safely released into the environment. Ensuring the various pieces of often expensive equipment are properly lubricated supports sanitation and saves taxpayer funds. However, increasingly complex machinery and shrinking budgets are putting the squeeze on plant managers.
In the town of Oconomowoc, Wisconsin, sewage treatment begins with several filtration steps to remove trash, sand and gravel, grease and oil.
The water receives most of its treatment during the aeration and activated sludge stage, in which biological degradation is accelerated to consume contaminants quickly. Secondary clarifiers then allow the activated sludge to settle and be pumped away, while the treated water is returned to aeration tanks. The water is then finely filtered, disinfected and aerated again to meet required oxygen levels. Additional steps and processes, such as water softening, may be added depending on local needs.
“You can’t discount the importance lubricants are to our facilities.”
– Tom Ryan, Metropolitan Water Reclamation District of Greater Chicago
|
And the work doesn’t stop there. The sludge must also be treated in preparation to be used as fertilizer on farms, in Oconomowoc’s case, or otherwise disposed of.
“You can’t discount the importance lubricants are to our facilities,” said Tom Ryan, chief operating officer at the Metropolitan Water Reclamation District of Greater Chicago, which includes seven wastewater facilities. Ryan, who runs one of the largest wastewater plants in the world, rattled off a long list of important equipment that needs lubricating on a regular schedule: electric motors, chain drives, air compressors, sewage pumps, clarifiers, speed reducers, and even the most simplistic U-joint. “Water reclamation is a complex process with a lot of moving parts that need lubricants,” he summarized.
Demand for water treatment is expected to increase as population growth and urbanization rise, along with awareness of its health and environmental benefits. Increasing water pollution and scarcity of water will also drive growth in the global industry, according to a report by Markets and Markets.
Wastewater treatment officials told Lubes’n’Greases that, especially in the United States and Europe, tightening rules on the industry and newer equipment have swept in more advanced lubricants. Long gone, they said, are the days when a 55-gallon barrel of grease would service all the machinery in a plant.
Most of the newer wastewater treatment equipment comes with recommendations for both lubricant brand and supplier, the managers said. While some pieces of equipment are decades old, new equipment warranties are often tied to using a certain brand and type of lubricant—something more than one manager complained about.
A few wastewater facility managers confirmed that they are ordering more types of lubricant than ever before. This increases the potential for mistakes, stock issues and other problems, pointed out Alain Noordover, business development manager for Gothenburg, Sweden-based SKF Group. “In general, too many lubricants are used in this industry because OEMs’ recommendations can be too strictly followed,” he said.
SKF makes bearings, lubrication systems, greases and other products for a wide variety of applications, including wastewater treatment.
Compounding Complexities
The types of lubricants needed within a treatment facility vary widely depending on the application and operating environment, Noordover told Lubes’n’Greases. For example, greases used in bearings operating at low speed under high load require a heavy base oil, mechanical stability and good extreme pressure and antiwear performance. For higher speed applications, low base oil viscosity, a higher temperature operating range and grease life should be considered. In other applications, corrosion protection for yellow metals such as brass can be important.
Some bearings and housings may be located under water, he continued, with potential water ingress leading to bearing corrosion. There, greases with outstanding antirust performance and water washout resistance should be selected, and biodegradability may also be required.
Synthetics have not yet made inroads in this industry, which leans heavily on mineral oil-based products, except in cases where lubricated parts may come in contact with water, such as slewing bearings in settlement tanks, Noordover explained. Biodegradable lubricants—mainly synthetic esters—are used in these applications.
Some OEMs are recommending more biodegradable greases for their assets, he continued. However, “I have seen in some plants that food-grade synthetic lubricants are being used in some applications with the idea of being more environmental friendly. Food-grade lubricants should not be mistaken as biodegradable lubricants,” Noordover cautioned.
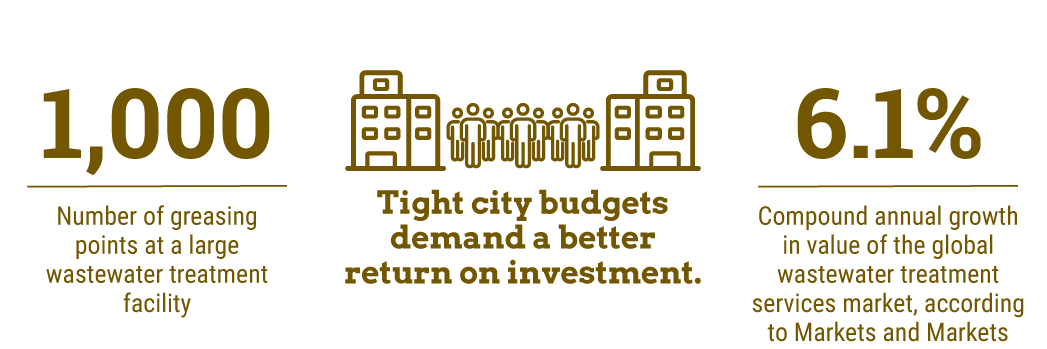
“I’ve been doing this for nearly 40 years, and the complexity of these lubricants has advanced to a point I never thought possible,” said one manager of a mid-size facility in the U.S.
In Chicago, approximately 17 billion gallons of wastewater flows through seven reclamation facilities daily. “I have no idea how much lubricant we use in a year because we use so many different kinds,” said Ryan. Several others echoed this sentiment.
In general, said Noordover, smaller volumes of grease are used at each greasing point, but a large plant could have more than 1,000 greasing points. Larger volumes of oil are used, mainly in small to medium gearboxes and pumps.
Plants Noordover has visited use about 50 to 100 kilograms of grease per year and around 500 to 1,000 liters of oil, packaged mostly in grease cartridges, 18-liter oil pails and single-point lubrication cartridges. The industry represents relatively low lubricant consumption compared to other industries such as paper mills and mining, he said.
“Virtually all applications can be covered by automation. The key resides in which is the best solution for which applications.”
– Alain Noordover, SKF Group
|
However, some management companies oversee many plants and pumping stations, which can add up to far greater volumes and even more complex maintenance schedules than individual plants, Noordover pointed out. “In a case we had, a group had around 900 sites to manage, including 12 main wastewater treatment plants, and the rest of small satellite stations located all over the country.”
To handle such varied lubrication requirements, some facilities are adopting automatic lubrication systems. “Virtually all applications can be covered by automation,” said Noordover. “The key resides in which is the best solution for which applications.
“For applications needing little lubricant and where points are quite distant from each other, single point lubricators make a lot of sense. For application where consumption is higher and many points are located at the same place, automatic multipoint lubrication systems would be preferred.”
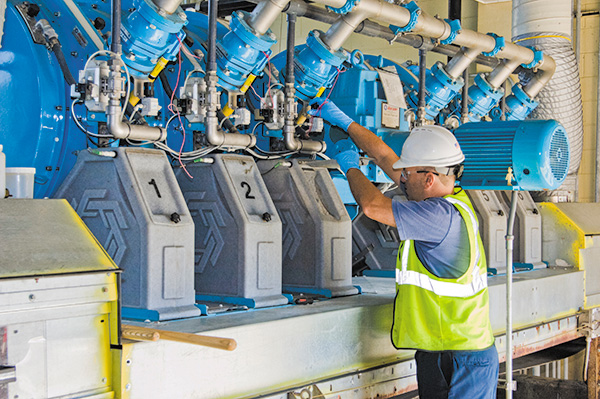
Automated lubrication systems help to ensure the right lubricant goes to the right place in the right amount, he said.
But not all plant managers are comfortable leaning exclusively on their automated systems. The New England manager said he feels better when his men are inspecting equipment manually. This, he said, allows workers to analyze the machine’s performance. If the equipment is using too little or too much lubricant, there could be a problem that needs an immediate fix.
In the near future, Noordover expects that internet-connected lubrication systems will become more widely available and will play a larger role in wastewater treatment. Such devices can provide the real-time status of lubrication needs and equipment health, enabling managers to make faster and better decisions. The systems are supported by online tools that assist in selecting the right lubricant and dispensing rate for a certain application based on its operating conditions.
Managing the Flow
Plant managers reported that the required understanding of chemistry and lubrication needed to work at a wastewater treatment facility makes recruiting new employees difficult.
“In my experience, I have seen general maintenance technicians taking care of lubrication in wastewater treatment plants,” said Noordover. “Due to the amount of tasks other than lubrication that they have to perform, lubrication might be neglected sometimes due to lack of time, skills or experience level.”
Operator-driven reliability programs may be considered, which would transfer some lubrication tasks such as inspections and basic greasing from maintenance technicians to operators. SKF and other lubricant companies and OEMs offer basic lubrication awareness trainings, according to Noordover.
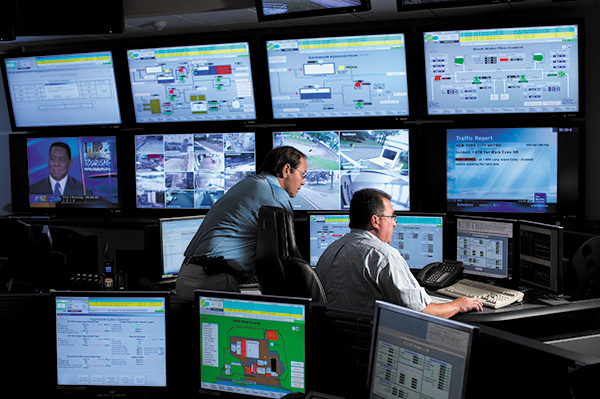
He offered some additional tips for plant managers to improve their lubrication programs:
- Creating a lubrication plan and schedule can help to ensure activities and knowledge are not isolated with skilled technician heads. Written procedures can also help operators and technicians transfer knowledge and ensure consistency of activities between different individuals.
- Making improvements to storage and handling of lubricants can help minimize the risk of mistakes and ensure that lubricants are kept in clean, dry conditions.
- A condition monitoring program, including use of predictive or proactive methods such as oil analysis and thermography in selected critical assets, can detect potential issues before they become a problem, prolonging equipment life.
“In order to approach lubrication in a more holistic way, it is important to conduct a lubrication assessment, which can help to draw a holistic picture of the current state of lubrication practices together with the most important improvement opportunities on people, technology and process levels,” he recommended.
All of the facilities managers agreed that keeping equipment properly lubricated saves money, an important consideration with tighter city budgets demanding a better return on investments.
Caitlin Jacobs is managing editor of Lubes’n’Greases magazine. Contact her at Caitlin@LubesnGreases.com.
Daniel Tyson was Senior Writer for Lubes’n’Greases.