The U.S. Air Force Civil Engineer Center’s Environmental Quality Technical Support Branch is leading a pilot study aimed at saving money and protecting the environment by changing its oil change procedures for engines used to power key systems on Air Force bases.
The study, estimated to save the military branch more than $1 million per year, utilizes a standardized oil testing service that provides enhanced analytics of oil samples. According to an Air Force press release, current regulatory drivers require each of the study’s five participating bases – Cheyenne Mountain Air Force Station, Peterson Air Force Base and Schriever AFB in Colorado, Joint Base McGuire-Dix-Lakehurst in New Jersey; and Seymour Johnson AFB in North Carolina – to analyze the oil in small engines annually and replace the oil completely at least every two years.
This frequency may be more than is necessary for many engines, said Frank Castaneda, air quality subject matter expert for the Air Force Civil Engineer Center in San Antonio, Texas.
The study dictates sampling oil from small engines at each of the five installations twice every year at $20 per sample. The samples are then sent to the testing service, which sends back a detailed analysis report in about a week’s time. Each respective installation incorporates its report into the Air Program Information Management System.
Castaneda told Lube Report that the study analyzes the viscosity, total base number and total acid number of oil samples, and also measures levels of water and wear metals such as aluminum, chromium, iron, copper, lead, tin, phosphorus and zinc.
Since oil that meets performance requirements may not need to be changed at the two-year mark, the study’s results can be used to extend oil life, reduce labor required to change oil and lower costs and environmental impacts associated with disposing of used oil and purchasing new oil, said Stuart Wallace, a contractor aiding Castaneda with the study.
In addition to manpower and cost savings, results from the study can also enable early detection of looming engine problems and help diagnose the root causes of those problems. For example, Donnie Ray, aircraft arresting systems manager at the 4th Civil Engineer Squadron at Seymour Johnson, explained that three engine oil tests failed because fuel was in the oil. This knowledge allowed for identification of problem units and made troubleshooting easier. “In another instance, we recently had a rear main seal go out, so we checked the previous report for metal particles,” Ray said in the press release. “In this case, there was no abnormal wear or underlying issues detected, so we could confirm it just needed a new seal.”
Engines from which the oil samples are drawn are reciprocating engines used to power emergency generators and electrical pumps for water, sewage or fire suppression systems, said Castaneda. The engines also do mechanical work such as rewinding aircraft arresting barriers or aggregate processing units.
Furthermore, Castaneda explained that the majority of engines encompassed by the study support emergency equipment and usually operate during interruptions to commercial power or during maintenance and readiness testing.
He stated that most of the engines used by the Air Force are diesel-powered, with a smaller number powered by gasoline or natural gas.
“As would be expected, the wide variety of applications these engines support leads to a wide variety of engine characteristics,” Castaneda told Lube Report. “The oil capacity for the engines across the Air Force varies from 1.2 gallons in very small units to over 300 gallons for the large utility-style engines that support high electrical demand systems.”
The lubricants used in these engines “are all commercially available [industrial] engine oils from a variety of manufacturers,” said Castaneda. “Examples include Shell Rotella 15W-40, as well as several products from the Mobil Delvac series.”
The study, initiated by Castaneda, launched in June 2019 and is set to end soon, at which point Castaneda will provide an overview of the report to the Air Force Civil Engineer Center Operations Directorate, which can then use the study’s findings to justify internal policy changes regarding oil change frequency.
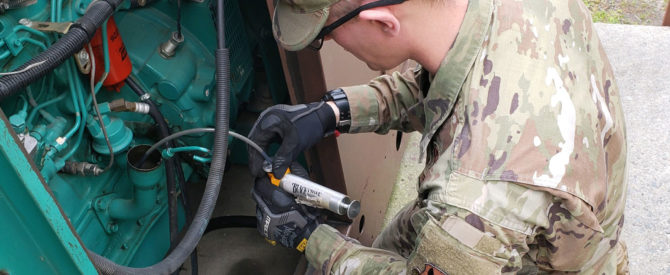
Senior Airman Zachary Goodwin, electrical power production journeyman, collects an oil sample from a small engine at Seymour Johnson Air Force Base, North Carolina. The sample is being collected as part of a pilot study to provide detailed analytics and potentially increase the lifespan of oil used in Air Force small engines.