Heat is the largest consumer of energy at any lubricant or grease plant and is used to reduce the viscosity of base oils and additives for pumping, improving mixing or facilitating chemical reactions. It is also used to remove byproduct water or methanol in grease manufacturing. For both lubricants blending and grease manufacturing, energy for heating is essentially fixed by the batch size, the product being blended and the heating technology.
The cost differences between current heating technologies—such as hot oil, steam or electrical trace heating—are often small compared to the cost per ton of product. The costs of change are high, though, since it includes significant capital expenditure, writing off equipment that may have many years of useful life remaining, or both. Savings on energy are marginal and difficult to accomplish without compromising product quality. Or so it has always seemed.
The past two years have seen the commercialization of two technologies that offer potential to change this by altering the means of transmitting energy into the fluid. Ultrasonic mixing of lubricants and microwave heating of greases during manufacture offer enormous energy savings, a safer working environment and other benefits. It cuts down on energy costs by transferring energy directly into the fluid, rather than indirectly heating a vessel or pipes that then transmit heat to the fluid.
Making Noise
Warrington, United Kingdom-based Blendtek Solutions has brought ultrasonic mixing to market as a scalable, energy-efficient mixing process. With three years of development and testing and nearly two years on the market, Blendtek Solutions’ system is remarkably simple. The key component is an ultrasonic cavity contained (in the smallest case) in a 5-foot tube with an external diameter of 8 inches. The footprint of the complete unit (cavity and control unit) is around 10 square feet, and the unit is about 5 feet tall.
However, it is the environmental footprint of the ultrasonic mixing that grabs attention, as the energy consumption during blending is very low. Alex Ball, sales manager at Blendtek Solutions, explained that “the energy requirements of our equipment are low: 1.5-3 kilowatts of electricity depending on the unit size.” This compares with megawatts that could be consumed when heating the componentry and the vessel for mid-sized batch blends.
In the same manner as ultrasonic cleaners used in laboratories and sold for domestic tasks like jewellery cleaning, the ultrasonic energy generates bubbles in the fluid that cause mixing as they travel through the fluid. Ball stressed that the shearing is excellent for mixing while still leaving polymers unharmed.
The power requirements of the equipment are so low, it can be connected to a domestic power socket or a small photovoltaic array. Blend times are very short—often less than an hour for blends that take three or more hours (and have been heated to 40°C or higher) in a conventional blending tank.
“This process enables the absolute minimum use of energy as the foundation of production, as opposed to current efforts that merely try to offset the environmental impact of lubricant manufacturing,” Mick Kenyon, operations and technical director at Witham Group, told Lubes’n’Greases. “We have saved over 26,000 tons of carbon emissions since using the process and saved energy that could have heated the equivalent of over 144 homes in the U.K. for a year. Our gas consumption has been reduced by just over 90%.”
Riding the Wave
A fire at Environmental Lubricants Manufacturing in 2007 provoked a significant rethink of how the company would manufacture its biobased greases. “During the post-fire research, it became evident that heat transfer oil fires were prevalent worldwide, but the focus was on prevention via proper maintenance and more effective fire suppression techniques,” Lou Honary, president
of Iowa-based ELM told Lubes’n’Greases. “The concept of using the built-in magnetic energy of molecules to excite them with the magnetic fields of radio waves to create frictional heat seemed most logical when looking for an alternative.”
High-temperature heat transfer oil was a factor in the June 2021 fire at Chemtool, which destroyed the largest grease manufacturing plant in the United States.
A decade after commissioning the first vessel, ELM’s subsidiary, WAVEtek Process Technology has now granted the worldwide marketing rights for grease processing technology using microwaves to Patterson Industries (Canada)—a division of All-Weld Company Limited [Patterson], located in Toronto, Ontario, Canada. ELM is also expanding its production and demonstration plant. “We are building the first grease plant incorporating over one megawatt microwaves to produce over 6,000 metric tons of grease annually,” Honary said.
Productivity Benefits
Both processes claim much shorter residence times in the vessels, thus improving the utilization of equipment and possibly staff, while further reducing utility costs. Blendtek Solutions equipment is mobile, with a small rinsing requirement (around 100 kilograms), so it can be moved between tanks that are dedicated to individual blends without risk of cross-contamination. Base oils and additives are charged to the tanks as usual, but the mixing takes place by circulating the blend through the ultrasonic cavity.
At Witham Group, a routine blend takes 20-40 minutes. “This has been the single most fundamental change to the way we manufacture lubricants in my 40 years and possibly ever,” Kenyon told Lubes’n’Greases. “Whilst the environmental impact of our business is at the heart of all we do, the speed and flexibility that this method allows has increased our production capacity four-fold without the need for extra blending vessels and other infrastructure.”
A very small batch can now be blended in the same packaging that is delivered to the customer. Blendtek Solutions’ website hosts a video demonstration of a 600-kg blend of an ISO 46 fluid in a plastic intermediate bulk container. The base oils are charged to the IBC, then circulated through the ultrasound cavity with the additives, which are pre-weighed into a decanting bucket. With almost no waste in the blending process and relatively high precision on batch sizes, both supplier and customer can reduce costs and minimize waste, burnishing the sustainability credentials of both.
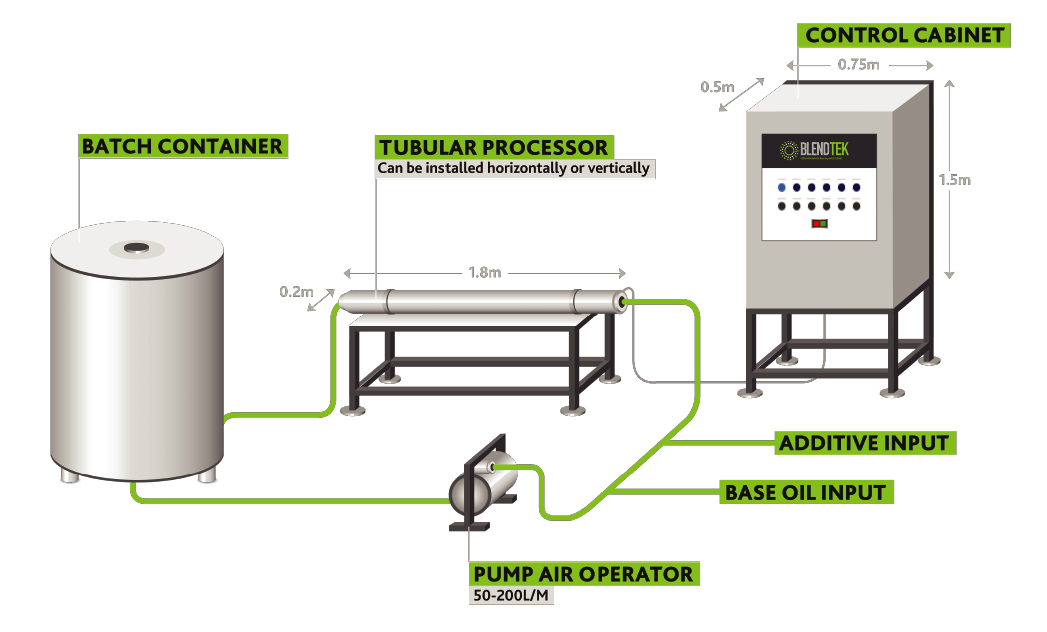
These processes are not just for smaller blenders. A small “blend to order” quantity is difficult for larger blenders used to working with batches of 50 tons or running their crankcase lubricants through inline blenders or other high-throughput equipment. The 600-kg specialist fluid can be a key requirement of some customers. But faced with such order quantities, companies either must have small tanks, which increase capital expenditure; blend to stock, increasing their working capital; pay for a toller, resulting in reduced margins; rebrand from a competitor, resulting in lost margin; or choose not to blend such a product, putting the company at risk of losing a customer.
Correcting blends is also a lower-energy process. Usually, the blend begins to cool prior to filling and during sample analysis. If a correction is required, the vessel may have to be heated again, and there will be a set time for agitation. Using Blendtek Solutions’ ultrasound equipment, the blend is at ambient temperature, so no re-heating is needed and the time to circulate the fluid through the mixer is shorter.
But what of viscous additives and base oils?
“The technology can be operated at ambient temperature, especially for base oils,” Kenyon said. “Some additives, depending on viscosity can require heating but only to make them pumpable.” Viscosity modifiers are generally introduced as liquid concentrates. Blendtek Solutions’ customers have applied the technology to viscosity grades from SAE 0W/ISO 32 up to ISO 680, meaning that the whole portfolio of many blenders can be handled by this equipment.
ELM’s microwave grease manufacturing process also claims reduced cycle times, reduced waste and a higher yield per unit thickener mass, as the thickener is more uniformly dispersed through the grease.

One of the most striking video sequences of the ELM process is a near-empty reactor with clean walls after grease has been pumped out. The grease is not oxidized by resting on hot surfaces and does not adhere to the vessel walls. This increases the chemical yield—the amount of usable product relative to that of the reactants. Greases produced by microwave heating tend to be paler than their counterparts, as they haven’t been degraded by overheating.
Overcoming Obstacles
It is received wisdom that you shouldn’t place a metal container in a microwave oven, but it’s not true in every case, as shown here. However, “arcing may occur if there are gaps between metal components where the waves could resonate,” Honary said.
Mixing paddles are needed when manufacturing higher-viscosity greases. These are carefully designed to avoid any gaps that could induce arcing. The shaft of the mixing arm could act as an antenna, allowing the microwaves to escape via the shaft ends. The solution is to use microwave chokes. The grid or screen in the glass window of a domestic microwave oven is a choke, where the size of the holes and the thickness of the grid are appropriate to choke the waves that try to exit through the holes.
Early vessels at ELM featured waveguides that brought the microwaves in to the top and circulation pumps or mixing arms to bring cool product from the bottom of the tank. More recently, ELM has developed a microwave window that allows the microwaves to enter the bottom of the vessel and still handle the pressure and vacuum of the vessel.
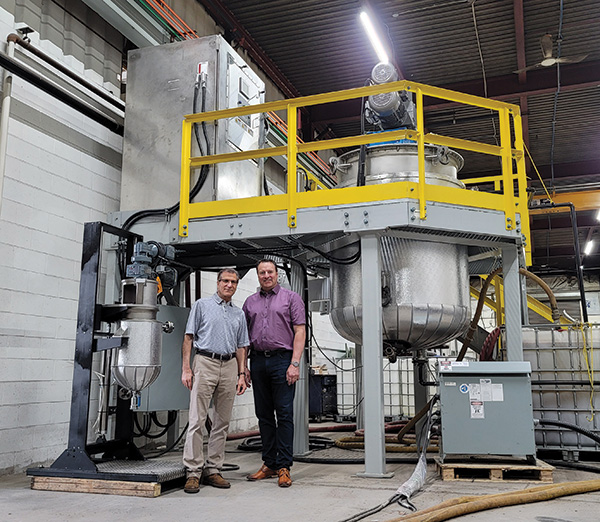
Microwave heating is ideally suited to biobased products, as the ester group of a fat or an acid group of a fatty acid presents a large dipole that interacts strongly with oscillating electronic and magnetic fields of the microwaves. This transfers energy to the molecule, which is converted to heat due to friction between that molecule and its neighbors. Mineral oils don’t have a significant dipole but can be heated by use of susceptors—either chemicals in the mix (such as the fatty acids to form the grease thickener) or surface coatings on the vessel.
Windows and susceptors have been fully incorporated into a Patterson kettle that has been under testing for almost a year.
User Benefits
Witham Group has been using Blendtek Solutions’ equipment for nearly two years. Simple blends take less than an hour to blend (a 75+% reduction), with productivity and customer responsiveness times improving. “Our overall inventory has reduced, given we can make exactly what we need as our customers need it,” Kenyon said. “The speed at which we can now manufacture has, by nature, allowed us to make more of our range ‘make to order’ than ever before without compromise to either quality or service.”

ELM estimates that most grease batches take 50%-66% less time and consume nearly 40% less energy than producing the same batches using conventional oil heating. In addition, the batches have higher yields per unit mass of thickener, less oxidation damage to the product and less scraping to clean.
Commercialization
Blendtek Solutions is making the rounds at industry meetings, while ELM and Patterson presented a grease kettle that utilizes microwaves for heating mineral oil-based greases at the annual NLGI meeting in June 2022. “We are very excited to team up with Dr. Lou Honary and ELM in what we believe will be grease industry-altering technology,” Scott Dunsmoor, president and general manager of Patterson Industries (Canada,) told Lubes’n’Greases. “The adaptation of ELM’s vast experience in the use of microwave technology in biobased greases to the development of our new mineral-based grease kettles using microwave technology will offer the grease industry significant options of which way they chose to invest in future expansions or new installations.”
Nigel Bottom, group managing director of Witham Group, is also very enthusiastic. “This exciting breakthrough is all about changing the environmental impact of lubricant manufacturing in the first place,” he told Lubes’n’Greases. “So many environmental schemes and businesses look to offset their impact by using carbon sinks and other environmental and climate protection projects. We have instead come up with a way that prevents…high energy use in the first place.”
Trevor Gauntlett has more than 25 years’ experience in blue chip chemicals and oil companies, including 18 years as the technical expert on Shell’s Lubricants Additives procurement team. He can be contacted at trevor@gauntlettconsulting.co.uk