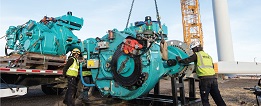
With costs exceeding $3 million for a 2-megawatt commercial wind turbine, operators have much incentive to take good care of their investments. Yet, no across-the-board industry standard exists for wind turbine lubricants, and performance demands for a given installation can vary widely by hardware and operating environment. The choice can leave operators bewildered, but using the wrong gear oil or grease could have expensive consequences.
An additive maker, a bearing manufacturer and an oil major shared their insights into formulating high-performance wind turbine lubricants-and what happens when operators use the wrong ones-during the National Lubricating Grease Institutes annual meeting in June.
Joe Kaperick, senior R&D advisor for greases at Afton Chemical, identified three key trends for wind energy during his presentation to the group gathered in Coeur DAlene, Idaho: larger turbine size, increasing offshore installations and policy uncertainties in some countries. The first is perhaps the most impactful. Todays wind turbines are producing nearly 20 times more power per turbine than those installed in 1990, the American Wind Energy Association estimates, and Kaperick believes such dramatic increases will continue. Right now, 1 to 2 megawatts are pretty standard, but 10-plus megawatt size turbines are becoming technologically possible, and they keep pushing these limits to generate more electricity more efficiently.
In March, GE unveiled the largest-to-date offshore wind turbine. Like many large turbines, the Haliade-X has a direct drive generator and a rotor diameter of 220 meters, which is roughly equal to two soccer fields. A single turbine could power 5,000 homes. These wind power giants are challenging traditional lubricant technologies.
Plenty is demanded from the lubricants that keep wind turbines turning. Greases, for example, must be able to flow through a centralized pumping system at minus 40 degrees Celsius in frigid mountains and stay in place above 50 C on sweltering open plains. They must also fight moisture from humidity, rain and seawater, providing corrosion protection and water resistance.
High dynamic loads and potential shock loads from changing wind speeds are challenges for all lubricants in a wind turbine, but different parts also have unique challenges. These include maintaining lubrication film at slow speeds and resisting fretting wear from vibrations in the main bearing; fending off fretting and false brinelling in the pitch system; and wear, scuffing and micropitting in the gearbox.
White etching cracks are the most recent issue identified for wind turbines, Kaperick said. The industry is elbow-deep in solving the problem, which can lead to pitting, spalling and bearing failure. (See LubesnGreases April 2018.)
To meet high levels of protection for long relubrication intervals, Kaperick has observed increased use of synthetic lubricants, as well as discussion about using specialty greases instead of multipurpose greases for particular parts of a turbine.
Blowing the Budget
Kaperick estimated that the installed cost for a 2-megawatt wind turbine is about $3 million. As a wind turbine operator, he said, youre not going to be too worried about the cost of the oil, but can it do the job? Can it protect my investment?
Greg Morris, grease product application specialist with Shell, recalled a wind farm that experienced catastrophic damage in 2009 due to a poor lubricant choice.
The original equipment manufacturer of the farms turbines recommended a multipurpose grease for both blade bearings and the main shaft bearing. The mineral oil based lithium grease could have, in theory, maintained sufficient film thickness-below 42 C (108 degrees Fahrenheit).
However, the wind farm was located in an area with historically hot weather. Operating temperatures inside the bearing would have exceeded 42 C at ambient temperatures of just 25 C. Historic data showed that on 62 percent of the days in a given year, temperatures inside the bearing would have passed the 42 C threshold.
When Morris team was able to assess the damage, wear was excessively high. Copper in the used grease hit 65,000 parts per million and iron 44,000 ppm. The bearing had pitting all along the surface, and rollers were severely damaged.
The turbines were no longer under warranty, and expenses included inspections and damage analysis as well as the cost to replace 60 to 70 pounds of grease per turbine with a fit-for-purpose synthetic grease.
The bearings in question should have lasted over 20 years, but Morris projected a lifespan of less than 25 percent of that. Each bearing would have cost $300,000 to replace, and there were hundreds of bearings on the farm. Loss of revenue during repairs was also significant. In the end, choosing the wrong bearing grease cost the wind farm owner over $40 million.
Testing for the Best Grease
Even with well formulated and properly selected greases, challenges still remain for additive solutions for different areas, particularly fretting and corrosion, Kaperick said.
ASTM D4170 (Standard Test Method for Fretting Wear Protection by Lubricating Greases) is still used to screen for fretting performance, but it is perhaps not the best test to use to look at fretting in a wind turbine, he suggested. A common fretting wear test that attempts to mimic field conditions, the Riffel test, is a very expensive, large, involved test, he explained.
Instead, Kaperick recommended that formulators consider using multivariate analysis to design the best wind turbine lubricants. Look at a model based on an easily run bench test that measures properties that could relate to fretting but arent directly correlated, he advised. Useful tests could include Fafnir fretting, a high-frequency reciprocating rig or SRV for corrosion, rheology, four-ball wear and oil separation tests.
Data from these tests can be used to build a formulation by changing particular properties. SRV friction results can be adjusted by tinkering with the friction modifier, and oil separation properties can be shifted with a polymer or the grease thickener. If you can adjust the three characteristics that you know are the most important, then you ultimately get something that helps with the wind turbine in the field, Kaperick said.
This approach is more difficult for corrosion protection, as most corrosion tests are pass-fail. But formulators can still study important factors related to corrosion and optimize formulations, he encouraged. For example, the alkalinity of an overall formulation can affect how its additives work. Grease makers should also understand the effects of time, moisture salinity and temperature in the field. Adjust the concentration of salt solution, time to run the test, temperature and other relevant factors to most closely resemble anticipated field conditions, Kaperick instructed.
Also, consider types of corrosion tests that give results beyond pass or fail, for example an admittedly subjective evaluation of the percentage of rust coverage, or optical methods like Average Gray Value, he continued.
Kaperick reiterated the importance of giving careful consideration to the type of test being used. In a study of two formulations of the same grease and different concentrations of salt water, he observed that the Emcor bearing test for corrosion was not as severe as a static bearing test.
That seems intuitively not right, he said. You have a dynamic bearing test that runs for a week versus a static test thats sitting there for 24 hours. So if youre running an Emcor thinking its more severe, and if it passes an Emcor then you should be good, maybe thats not the right correlation for your application.
At the same time, consider the effects of other surface active additives that may be competing against the additives being adjusted, he said. Factor in, for example, the impact of rust inhibitors on other aspects of performance such as fretting. Maybe youve got a good rust inhibitor, but its preventing good wear protection, Kaperick cautioned.
Chemical synergy among additives can also be beneficial. Combinations of rust inhibitors often work much better than any rust inhibitor by itself, he reminded.
If someone presents you with, Heres my spec for wind turbine and you just need to meet this, question that and talk about what they really need versus what theyre measuring, he concluded.
Defining the Best Grease
Kuldeep Mistry, lubrication lead at wind turbine bearing manufacturer The Timken Co., pointed out that commercially available greases for the wind industry vary significantly in consistency, viscosity, base oil type and other properties. With such high stakes for lubricant performance, Timken customers were requesting main bearing grease recommendations.
Mistry and his team first identified key characteristics for wind turbine main bearing greases: wear protection, service life, low-temperature performance and water handling capabilities.
Timken conducted testing to evaluate those key properties, recommended specifications for each performance parameter and ranked the criteria by importance. Top of the list was wear protection for bearing rollers and cages. Next was oil separation, followed by false brinelling and fretting protection. Additional priorities are listed in the table on page 40.
The researchers then investigated grease formulations. They tested a selection of 13 mostly lithium based greases, then chose some to review in greater detail.
Investigation of elastohydrodynamic lubrication film thickness concluded that higher base oil viscosity is preferred in order to obtain higher lubricant film thickness that can protect bearings during operation.
The researchers used a Wedeven Associates Machine (WAM6) to test for traction coefficients and Stribeck curves at different speeds and temperatures using 52100 steel balls and polished discs with 2 gigapascal load. Several slide-to-roll ratios were tested, mimicking different types of bearings. For example, taper roller bearings operate at about 1 percent slide-to-roll ratio, cylindrical roller bearings at 5 percent and spherical roller bearings at 12 percent.
The traction coefficients for different greases were different at different slide-roll ratios, and it was lower for taper roller bearings, Mistry reported. Within a particular ratio, though, traction remained consistent at different speeds. Ultimately, these tests showed that base oil selection for a grease affects its traction coefficient: Greases with synthetic base oils had lower traction coefficients than either mineral or semi-synthetic greases.
Torque, temperature and migration studies showed that grease selection also influences these factors. Grease must remain on bearing surfaces during operation to ensure there is enough oil to form a protective lubrication film. With greases that migrated out of the roller raceway, researchers observed higher traction coefficient and higher temperatures, Mistry noted. However, a residual oil film remained on the rollers and raceway.
Mistry pointed to the importance of overall grease formulation, not just base oil properties, to produce the best results. For example, a high-viscosity base oil used in one of the tested greases caused 75 percent higher torque and 15 percent higher bearing outside diameter temperature than a low-viscosity base oil used in another tested grease. However, the two formulated greases had similar torque and temperature results in the test because the grease with high-viscosity base oil migrated out of the bearing.
Base oil viscosity is a big driver of lubrication film thickness, and base oil type is a big driver of traction coefficient, Mistry summarized. But theres a huge role of overall formulation which governs grease performance, he concluded.