
As original equipment manufacturers continue to push the limits of efficiency in modern hydraulic equipment, today’s hydraulic fluid formulations must demonstrate high performance under tough conditions. The right formulation can help deliver higher efficiency and robust protection and can lower the overall cost of ownership for end users.
The ongoing pursuit of new efficiency gains has seen mobile and stationary hydraulic systems undergo major changes in recent years. The dramatic technological changes OEMs have developed have implications for all parts of modern machinery. Of particular importance are hydraulic fluids that help such machines perform their duties.
Today’s hydraulic fluids must contend with more severe operating conditions than ever before, including higher temperatures and pressures that have resulted from increasingly common hydraulic equipment design changes. Because of this, traditional hydraulic fluid formulations may fall short of meeting modern demands.
To satisfy the needs of evolving equipment, hydraulic fluids must be formulated more thoughtfully than in the past. Formulators must consider new chemistries and polymers that can provide higher levels of performance and must communicate the necessity of such performance to end users. The truth is that optimized fluids can in fact reduce the total cost of ownership of hydraulic equipment via better stay-in-grade shear stability, optimized operating temperatures and improved energy efficiency.
This article will explore how new equipment designs impact the performance needs of modern fluids as well as how to optimize critical performance parameters with the right formulation approaches.
Challenging New Conditions in Modern Hydraulic Equipment
Today’s hydraulic machines are smaller and lighter than ever before, and a few drivers have made that the case.
The first factor is cost control. Hydraulic equipment OEMs have prioritized doing more with less, designing their equipment to require as few materials for construction as possible. By using fewer materials to construct a machine that provides the same levels of performance as a heavier machine, the OEM can save on raw materials costs.
The second intertwining driver is efficiency. A smaller, lighter machine that can do the same work as a bigger, heavier machine is fundamentally more efficient, requiring less fuel to perform the same function. Downsizing has been an attractive method for OEMs in many industries to eke out greater efficiency gains wherever possible.
How do these factors impact the hydraulic fluid? One of the primary targets of OEM downsizing has been the hydraulic fluid sump, where the fluid is stored before it is circulated throughout the machine. Traditionally large and heavy, designers discovered that reducing the sump size was highly effective as a means to meet their cost and energy savings goals.
However, a smaller sump fundamentally means that a lower volume of hydraulic fluid must be used to perform the same functions as a machine with a larger sump. Because of this, more severe operating conditions are created. The fluid will become hotter throughout its use, and because there is less time for the fluid to cool in the sump between circulation routes throughout the machine, the fluid will remain hotter for prolonged periods.
Excessive, prolonged heat can compromise the hydraulic fluid’s ability to perform its essential functions. The hotter a conventional hydraulic fluid becomes, the greater its potential to lose viscosity. Furthermore, as protective film layers become thinner and thinner as the fluid shears under more stressful operating conditions, the fluid’s protective capabilities can become compromised. Over time, this can lead to significant wear among moving parts of the hydraulic system, which can cause major operational issues and downtime for end users.
Sustained hotter temperatures can also cause conventional hydraulic fluids to oxidize more quickly. As a fluid oxidizes, its protective capabilities are further diminished, compounding the potential for major equipment breakdowns.
Finally, extensive and elevated heat levels in any part of the hydraulic equipment will necessarily cause said equipment to age more quickly.
Developing Fluids Capable of Meeting Modern Hydraulic Needs
As the needs of evolving hydraulic equipment change, it is clear that modern hydraulic fluids must be able to keep pace. Formulating today’s fluids with the right combination of performance polymers will be necessary to deliver the full range of performance attributes that can help today’s equipment operate as efficiently and reliably as possible over the long term.
To those ends, Lubrizol has recently identified an energy-efficient ethylene-propylene copolymer—referred to as OCP—that has the potential to significantly enhance key performance characteristics in modern hydraulic fluids. To demonstrate and validate this potential, Lubrizol’s testing teams compared three experimental ISO 46 formulations:
- Monograde (baseline). A conventional monograde fluid with no performance polymer.
- Formulation PP1. A multigrade fluid formulated with OCP.
- Formulation PP2. A multigrade fluid with polyalkyl methacrylate (PMA), which is a more conventional polymer additive.
Each of these formulations were tested across numerous benchtop viscosity and tribology instruments, total hydraulic system test rigs, and in real-world mobile and stationary hydraulic equipment. Lubrizol’s results were significant across a range of important performance attributes.
Stay-in-grade shear stability. Formulation PP1 outperformed the conventional monograde and formulation PP2 in terms of shear stability across multiple tests. PP1 excelled in benchtop KRL shear tests, maintaining its viscosity across hundreds of hours (See Figure 1).

Similar results were recorded in OEM pump testing. PP1 exhibited low levels of viscosity loss throughout the test, further demonstrating its ability to maintain shear stability across a range of challenging operating conditions. Finally, in field testing, PP1 further validated its ability to retain parts-protecting viscosity in tough, real-world environments.
Energy efficiency. Next, Lubrizol’s teams sought to validate the OCP’s ability to improve the efficiency of hydraulic fluid formulations. The company evaluated three experimental formulations in controlled experiments within Lubrizol facilities and in climate-controlled, off-site laboratory settings. This was done across a range of common hydraulic work cycles. In each cycle, PP1 demonstrated clear efficiency gains compared with the conventional monograde baseline.
These work cycles included the following:
- Laden lifts (2.0% efficiency gain)
- Front unladen lifts (5.8%)
- Mixed duty cycles (3.0%-4.0%)
- Backhoe loader (2.0%-5.8%)
- Wheel loader (1.4%-2.7%)
- Injection molding (8.5%)
PP1 accomplished these gains by improving the fluid’s secondary flow properties. Secondary flow areas are where the fluid is moving in a different direction to primary flow and are commonly induced where flow is constricted or changes in direction. Secondary flow can thereby prevent the fluid from moving as effectively and efficiently as possible.
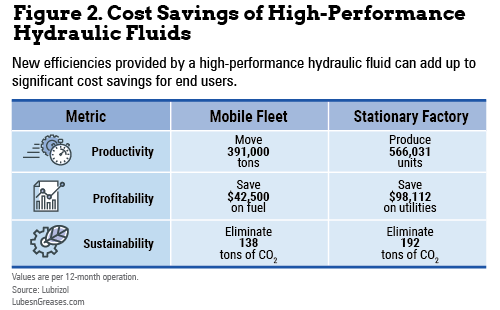
PP1 polymers were shown to form flexible, smaller-diameter chains with respect to their overall contour length, granting this formulation heightened viscoelastic behavior. Comparatively, PP2 polymers have long side-chains and comparatively short backbones that prevent tight coiling and reduce flexibility. PP2 has smaller extensibility and no detectable viscoelastic component. PP1’s viscoelasticity is effective in mitigating secondary flow.
Operating temperatures. Finally, in laboratory pump testing that evaluated Lubrizol’s fluids’ performance relative to each other, thermal imagery cameras captured a difference in surface temperature of approximately 3 °C, suggesting significantly cooler operation within the pump using the PP1 fluid. In a full-scale mobile hydraulic field trial, similar results were recorded. Hydraulic sump temperatures were reduced by an average of 4 °C over eight months of operation when using PP1, with even greater reductions in peak temperature spikes observed (See Figure 3).

The molecular structure of the performance polymer in PP1 generates less heat-inducing fluid friction, or traction, throughout the hydraulic system resulting in cooler operation and ultimately longer fluid and equipment lifetimes. More moderate temperatures over a sustained period of operation help mitigate the concerns around heat-related viscosity loss and premature oxidation. With these problems mitigated, a high-performance fluid will maintain its protective and performance properties over longer periods of time, helping to protect the equipment.
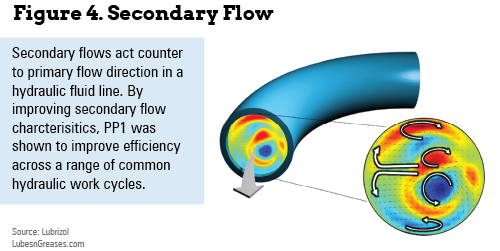
High-Performance Fluids Can Make a Meaningful Difference for End Users
By improving shear stability, mitigating extreme operating temperatures and improving energy efficiency of the machine, a high-performance hydraulic fluid has the potential to deliver true operational benefits for end users. Annually, Lubrizol’s estimates suggest that such a formulation can help equipment move hundreds of thousands more tons, save tens of thousands of dollars on fuel and utility costs, and eliminate hundreds of tons of carbon dioxide generation. Additionally, by reducing the need for excessive, labor-intensive maintenance, these fluids have major potential to help operators significantly reduce their total cost of ownership. These can all be major bottom-line impacts for any organization.
These are real benefits that hydraulic fluid formulators can deliver to their customers when they seek the right additive and polymer chemistry. To be certain, hydraulic equipment will continue to evolve in new ways. Fluid formulators will continue to be required to think outside the box. Work with your additives supplier to identify the best path forward and to continue delivering on the needs of modern hydraulic equipment.
Blayne McKenzie is technology development manager, industrial products for The Lubrizol Corp.