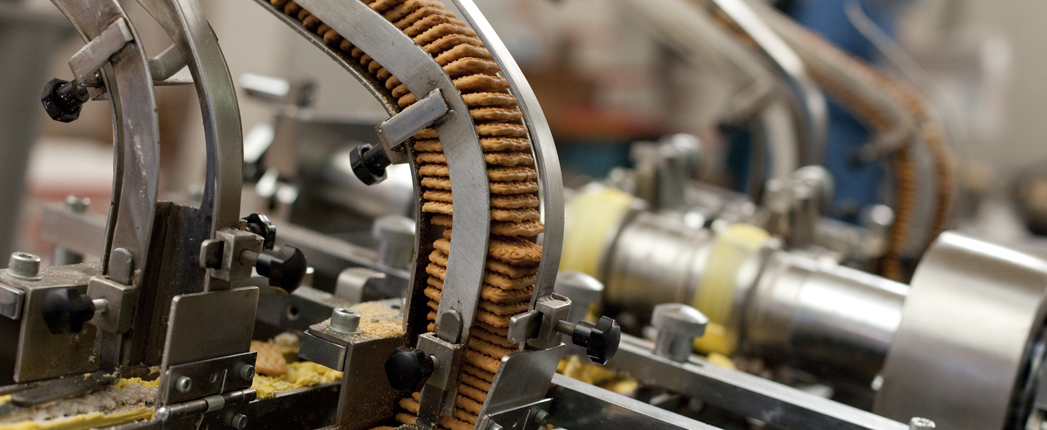
Regulations Ramp Up for Food-grade Lubes
COVID-19 may have caused widespread disruption this past year, affecting output and pushing the supply chain to its limits—but food production and processing have had to carry on despite the challenges.
Lubricants have helped ensure that ovens, conveyors, mixers and other equipment continue operating efficiently, effectively and safely.
The unforgiving environment of food production requires much more besides the usual resistance to wear, corrosion and extreme temperatures required by conventional lubricants. Food-grade products need not only to endure the typical stresses and strains of heavily used machinery, but they must also provide optimal protection against bacteria, water, dust and any other forms of potential contamination.
Specifically, this vital segment of the industry must guarantee there is no risk to human health should even a small amount of lubricant come in contact with the food itself.
“Although not intended to be a food ingredient by any means, these lubricants are intended for incidental contact,” said Orsi Dezsi, business unit manager for nonfood compounds & food contact material services with NSF International.
“Over the past year, food manufacturers have aggressively ramped up production for consumers so they can stock their pantries, freezers, refrigerators and cupboards. We’ve seen manufacturers adding more shifts and increasing production, so it’s fair to assume that their machinery has been running a lot longer and at higher capacities. That means there has probably been a significant increase in the use of food-grade lubricants, too. They really are an essential part of keeping the equipment and these facilities moving,” Dezsi added.
NSF International took over from the U.S. Department of Agriculture as the custodian of the voluntary H1 standard over 20 years ago and now conducts thousands of formulation reviews annually to ensure formulations meet all required standards and are acceptable for incidental food contact.
“The food-grade lubricant industry deserves a lot of kudos for its focus on safety and is really active in monitoring the regulations and being part of the discussions,” Dezsi said.
She also noted that H1 registrations climbed by 9% in 2020. Over the past year, 150 more manufacturers have been included in NSF’s online directory, and over 5,000 products have been added across all its categories. Its White Book listing (www.nsfwhitebook.org) is updated nightly, detailing suppliers and their approved products. Almost half of these are food-grade lubricants, she added.
Although H1 is the de facto standard for lubricants worldwide, it remains a voluntary program. There is also ISO 21469, which requires suppliers’ formulations to go through more vigorous testing and audits, but given the demands and requirements of modern food manufacturing, many have speculated that more stringent regulation may soon be on the horizon.
The National Lubricating Grease Institute’s Food Grade Lubricants Working Group convened virtually in April to discuss the robustness of the H1 regulation and the potential implications of more requirements being introduced. It also considered how the sector could collaborate more closely with other stakeholders in the future.
“We all know that in certain processes, it’s inevitable that a small amount of lubricant can get into the food, but legislators are starting to question this more and more,” said Andre Adam, European Lubricating Grease Institute board member and chair of the Food Grade Lubricants Working Group. “I don’t think we, as an industry, have all the answers right now.”
Adam continued, “I think that we need to work much more closely with food producers and legislators to share knowledge and highlight the importance of mechanical food production. The food industry is global, and this is a global issue.”
“We all know that in certain processes, it’s inevitable that a small amount of lubricant can get into the food, but legislators are starting to question this more and more.”
– Andre Adam, European Lubricating Grease Institute
|
Lawmakers in Europe are increasingly scrutinizing the products and components that come into contact with foodstuffs. Questions continue to be raised about the suitability and necessity of some of these chemicals used as part of the food production process.
There remain concerns about Non-Intentionally Added Substances and their potential effects on public health, said Adam.
The EU has long been calling on greater scrutiny on mineral oil saturated hydrocarbons and mineral oil aromatic hydrocarbons, and years have been spent investigating the potential risks.
Titanium dioxide has also been in the spotlight and has been banned as a whitening agent in France, while so-called forever chemicals polyfluoroalkyl substances are now being closely monitored because of their potential risk to human health and the environment. PFAS offer water, oil and grease resistance in food packaging such as boxes, bags and wrappers.
Any future proposals by legislators could be an expensive proposition for the lubricants sector, said Adam. The process of toxicity testing and an in-depth analysis of ingredients alone may prove extremely costly for base oil producers and the food industry, potentially impacting the viability of operating in this particular market.
“In Europe, the lawmakers don’t talk about lubricants; they talk about the individual components,” Adam said. “A lubricant is composed of maybe 10 different components, including multiple base oils and additives. I would expect the cost involved to carry out a full toxicology screen of additives is beyond what most companies could afford. This is an enormous undertaking that is expensive and time consuming. We, as an industry, are not fully aware of the problems ahead of us.”
“I would expect that users will soon start demanding even more information and want guarantees that certain components are not included in the lubricants,” he added. “There’s a lot of activity right now, with studies looking at Non-Intentionally Added Substances and the transfer from packaging material, printing inks and so on. These products all contain hydrocarbons and are already being specifically named as being banned from use. These are under the spotlight, and lubricants will come into focus eventually.”
Change may be inevitable, and new rules and regulations will likely come sooner rather than later.
In this Spotlight, Anderol and Zschimmer & Schwarz consider why selecting the right food-grade lubricants can make all the difference.
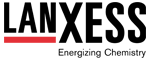
Selecting the Right Food-grade Lubricant for Your Compressor
With many food and drink processors running their production 24/7, compressor equipment needs to provide optimal reliability and performance with minimal downtime. It is essential that the right lubrication is applied.
Compressed air is a key energy source, trusted across the food and beverage industry for all aspects of production and processing—from transport and processing of raw materials through to the final stages of packaging and bottling. Clean and contaminant-free compressed air is vital.
Growing awareness of the importance of food-grade lubricants for consumer safety and Hazard Analysis and Critical Control Point (HACCP) regulations triggered an increasing demand for high-performance food-grade lubricants.
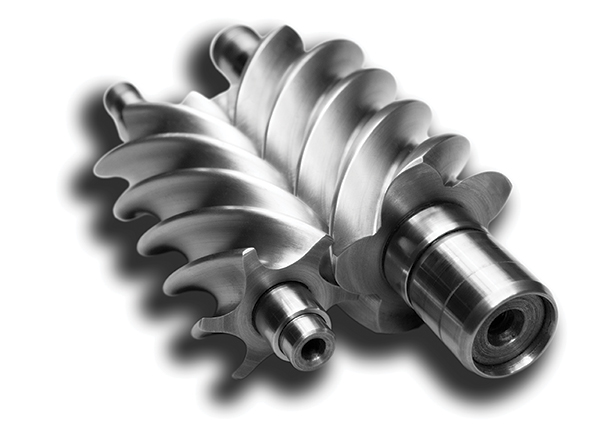
Selecting an appropriate lubricant for your compressor that boasts the specific properties can be difficult. The right solution means considering consumer safety and enhanced performance, while also helping to reduce maintenance costs and downtime.
Standard mineral oil is unable to meet the greater demands that are now being placed on air compressor lubricants. Anderol® semi-synthetics and synthetics have excellent thermal oxidation stability, allowing for long machinery service intervals. The Anderol® lubricants portfolio offers a fitting solution for every lubrication problem.
The following offers a Good, Better, and Excellent guide to selecting the most appropriate food-grade compressor lubricant for your equipment:
Good: Semi-synthetic Lubricants
Semi-synthetic food-grade oils offer an attractive blend of low cost and good performance. These are formulated from synergistic blends of severely hydrotreated, hydrocracked (Group III) base oils to provide a more refined, high-quality product.
They are enhanced with premium synthetic esters and proven additive technology, which help to improve viscosity, wear resistance at higher temperatures, and stress levels, as well as increasing their detergency properties—resulting in clean machinery lubrication. Semi-synthetic oils can easily last up to 4,000 hours, twice as long as the 2,000 hours achieved by standard mineral oils.
The semi-synthetic Anderol® FG S Series offers some of the most desirable characteristics of a premium synthetic lubricant at a significantly lower cost. This makes it an economically attractive choice for customers looking to take advantage of the benefits of synthetic oils over mineral oils without additional costs.
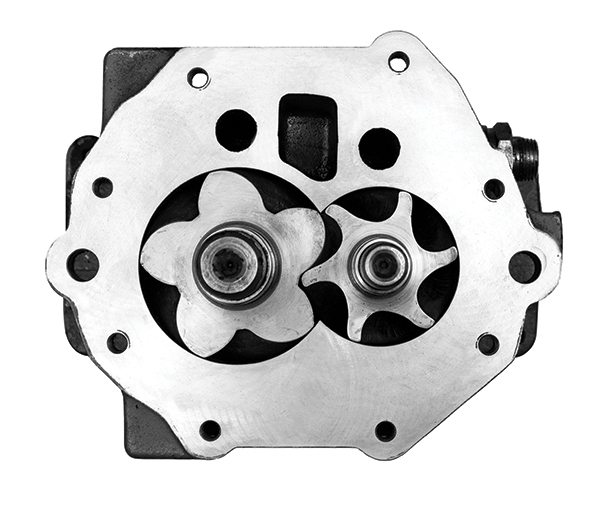
Compatibility is assured with Anderol® FG S Series lubricants, and there is no need for special precautions when switching from a mineral oil-based lubricant for use with paints, seals, gaskets and hoses. The Anderol® FG S Series for food-grade applications is available in ISO VG 32, 46, 68 and 100.
Better: PAO-based Synthetic Lubricants
Synthetic lubricants offer excellent levels of performance and have many advantages over mineral oil lubricants. Rotary screw compressors, in particular, require a synthetic lubricant.
Polyalphaolefin (PAO) based lubricants are most suitable for compressors, and they offer a series of advantages such as high-temperature thermal and oxidative stability, high flash point and low volatility, as well as being hydrolytically stable.
Anderol® FG XL Series is a high-performance synthetic food-grade lubricant with improved detergency for compressors and vacuum pumps. Its nominal operating range is -40°C to 170°C, and the performance time is up to 8,000 hours. Anderol® FG XL Series is available in ISO VG 32, 46, 68, 100 and 150.
Excellent: PAO/Ester-Based Synthetic Lubricants
Companies are increasingly balancing efficiency and sustainability. Machine operators expect longer machinery service intervals and therefore longer-life compressor lubricants. Longer oil life properties result in simply fewer production stops, a higher production output, less oil consumption and reduced waste.
Anderol® SYNcom FG HiPerf Series are extreme long-life synthetic rotary screw compressor lubricants. This PAO/ester-based lubricant offers the best of a PAO base, enhanced with a special ester to take additive solubility and the detergency of the whole formulation to a completely different level. This results in very low deposits and cleaner machinery, which improves the lubricant’s longevity and machine life.
Anderol® SYNcom FG HiPerf 46 offers excellent viscosity to temperature behavior, has a wide operating temperature range (-40°C up to 240°C peak temperature), very low evaporation loss (<0.01% at 100°C) of 22 hours, according to ASTM D972, and a very good film strength. This oil can last an entire maintenance cycle.
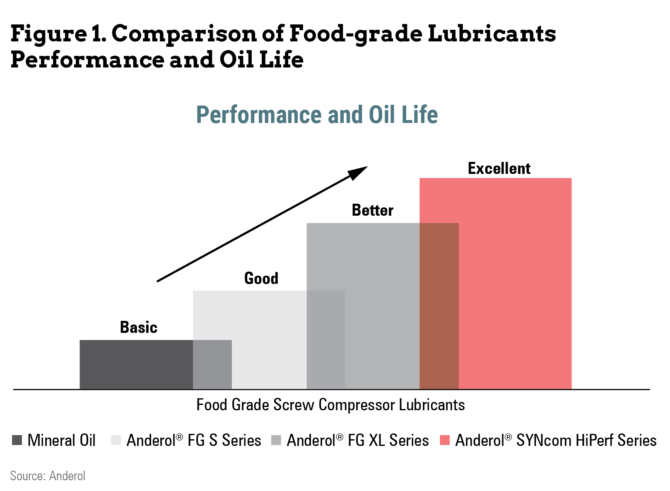
Extreme Environments
Very humid and acidic environments require a special lubricant that does not hydrolyze at high temperatures, form sludge or attack the seals and paints.
To meet these requirements, the lubricant additives business from LANXESS has developed C-NRT FGC for compressors and C-NRT Plus FG for vacuum pumps under the Anderol® brand, which are inert to the reactive gases found in the more challenging compressor and vacuum environments. Anderol® C-NRT lubricants are full cyclic aromatics or mixed with a synthetic hydrocarbon base specially formulated to increase service life in aggressive environments.
Not only will this product withstand attacks of aggressive gasses and resist rapid breakdown, it is also capable of keeping the deposits in solution, which has not been seen with any other mineral-, ester- or PAO-based product in these circumstances. The thermal and oxidative stability of the base fluid together with oxidation inhibitors extends the lubricant life at elevated temperature conditions.
Anderol® C-NRT products do not degrade at the same speed as other lubricants in harsh conditions, thereby dramatically increasing the service life of the compressor or pump. They are specifically designed to provide inertness and long-term lubrication in applications where contact with (reactive) chemistries cannot be avoided. Thanks to its excellent detergency effect, deposit/lacquering formation is avoided.
Delivering Cost Savings
Synthetic high-performance compressor lubricants offer significant savings. Although the cost of synthetic lubricants may be higher, their benefits offset the initial costs to offer an excellent return on investment.
Oil and filter replacement is minimized, disposal costs are reduced, and less maintenance brings down expensive labor costs. In addition, Anderol® improves machinery protection, reducing production stops and downtime and increasing productivity and output.
All Anderol® Food Grade Compressor lubricants are NSF H1 Registered, produced in an ISO 21469-certified plant and are Kosher and Halal certified.
|
All Anderol® Food Grade Compressor lubricants are NSF H1 Registered, produced in an ISO 21469-certified plant and are Kosher and Halal certified.
Anderol® is a specialty lubricants product line and brand within the Lubricant Additives Business Unit (LAB) from LANXESS. Anderol B.V., the European producer of Anderol® products, is a wholly owned subsidiary of specialty chemicals company LANXESS.
Anderol B.V., the European producer of Anderol® products, is a wholly owned subsidiary of specialty chemicals company LANXESS, and has a proven track record and over 80 years of experience specializing in compressor and food-grade lubricants. Find out more about our food-grade lubricants and our customized solutions at www.anderol.com
This information and our technical advice—whether verbal, in writing or by way of trials—is subject to change without notice and given in good faith but without warranty or guarantee, express or implied, and this also applies where proprietary rights of third parties are involved. Our advice does not release you from the obligation to verify the information currently provided—especially that contained in our safety data and technical information sheets—and to test our products as to their suitability for the intended processes and uses. The application, use and processing of our products and the products manufactured by you on the basis of our technical advice are beyond our control and, therefore, entirely your own responsibility. Our products are sold in accordance with the current version of our General Conditions of Sale and Delivery.
©2021 LANXESS. Anderol®, LANXESS and the LANXESS Logo are trademarks of LANXESS Deutschland GmbH or its affiliates. All trademarks are registered in many countries in the world.

LEXOLUBE Lubricants Range Provides Food for Thought
Zschimmer & Schwarz and its LEXOLUBE® brand has established itself as a leading supplier of lubricant ingredients for the food processing industry, producing a selection of high-quality HX-1 synthetic ester base stocks, including Kosher/Halal-certified options.
LEXOLUBE products are ideal for high-performance applications in demanding environments, whether high-temperature oven chains or compressor units.
“We’ve developed a really strong portfolio of products over the years that are used across the food processing industry,” says Tyler Housel, Director of Sales – LEXOLUBE. “In this market, safety and performance are everything.”
“We started making commercial sales about 10 years ago and were the first to introduce HX-1 synthetic esters that met the unique performance characteristics that were required. This remains a key segment for us and end-user demand continues to grow.”
The LEXOLUBE® FG-HX1 range consists of high-performance synthetic polyol ester base stocks used to lubricate food processing equipment. These boast excellent thermal/oxidative stability, low volatility, high flash points and low-temperature fluidity.
Driven by increasing industry concern for food safety assurance, Z&S is further enhancing its offerings of food-safe synthetic esters that are used to formulate high-temperature oven conveyor chain oils, long-life compressor lubricants, greases and fire-resistant hydraulic fluids that carry NSF International’s H1 registration.
“We’re expanding our portfolio to meet the current demand for H1 and HX-1 products and the needs of the modern food processing world,” adds Housel.
“Mineral oil has been around forever and does a lot of great things, but there are some applications where it falls short and can’t hit the performance or safety requirements. There are certain times when synthetic esters are needed. We’ve therefore spent a number of years building our range to include high performance products that better serve the food processing industry.”
Hydraulic fluids, in particular, are a key area of focus moving forward, he says. Zschimmer & Schwarz also recently launched the next generation of high-temperature chain lubricant that provides longer relubrication intervals, better wear protection and less residue formation.
For more information about the Lexolube range of food safe esters, visit www.zslubes.com